Offset Printing
6 ways BOBST is staying ahead of the market in flexible packaging
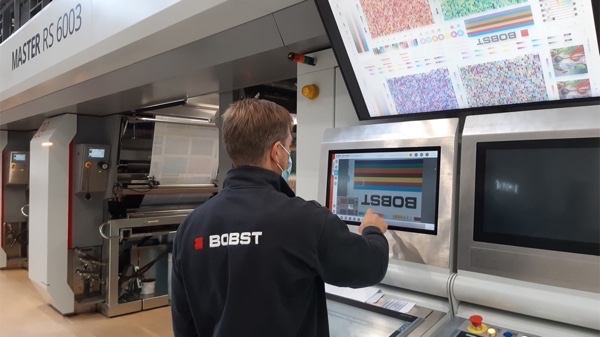
Friday 21. January 2022 - The leadership that we have achieved today has not happened by chance. We have always assessed future market trends and adapted accordingly to stay ahead of them, while maintaining a consistent focus on high quality products and strong customer relationships.
Sara Alexander, Flexible Packaging Industry MarCom Manager at BOBST is talking about what has kept the company at the forefront of the packaging production market for over 130 years.
Founded in 1890 by Joseph Bobst in Lausanne, Switzerland, BOBST now has a presence in more than 50 countries, runs 15 production facilities in 8 countries and employs more than 5,500 people around the world. It is still run by a member of the Bobst family: Jean-Pascal Bobst, CEO of the Bobst Group, represents the fourth generation of the Bobst family in the company.
A major step for BOBST was moving into the flexible packaging market in the 1980s. These days of course, flexible packaging is a booming market, but one of constant change and evolution.
So, how has BOBST managed to build and consolidate its success in this area?
1. Making strategic acquisitions that add real value
In 1987, BOBST made its first foray into flexible packaging, buying a 50% stake in the share capital of the Italian machine manufacturer Schiavi Cesare Costruzioni Meccaniche SpA in Piacenza.
Since then, several other strategic acquisitions have added know-how and experience in flexible packaging. Just recently for example, BOBST completed the acquisition of Cerutti, a world-renowned manufacturer of rotogravure printing presses, consolidating its technology and market presence in the global gravure printing market.
Of course, acquisitions alone are no guarantee of success. BOBST fosters a culture enabling development of its own innovations in the flexible packaging industry, backed by significant and consistent R&D investments and a strong vision of the future.
2. Delivering the complete package for converters
There is huge added value in being able to offer solutions across the entire flexible packaging chain.
Uniquely, BOBST can be a single source supplier, with solutions can address all needs: from the file and the product specification, through to all production steps on BOBST equipment until the final product, for all flexible packaging substrates and applications.
All BOBST equipment and services – which are founded on four key pillars that are driving the current packaging industry: automation, digitalization, connectivity, and sustainability – create value for the users, and enable more agile and profitable printing and converting.
“Offering all technologies for production of flexible packaging means that we can approach each customers challenge from an end-to-end view and develop the solution that best fits the given requirements at every stage of the production process,” comments Sara.
3. A true commitment to sustainability
Environmental and sustainability issues are at the top of the agenda of governments, companies and individuals all over the world.
We know that the qualities that make plastics so suited for packaging – versatility, durability, impermeability – also make them very environmentally unfriendly; non-biodegradable and challenging to recycle. It is a particular challenge for flexible packaging such as that used for food packaging, where the high barrier protection against oxygen and water that prevents deterioration is currently provided by multi-layer, multi-material packaging, which cannot be recycled.
BOBST has pioneered multiple solutions that enable better sustainability in production, equipment and processes.
Together with its partners, BOBST has launched samples of high barrier flexible packaging solutions designed for recyclability, taking us one step closer to the ultimate goal of being able to provide completely recyclable solutions to replace non-recyclable packaging.
BOBST is also now introducing oneBARRIER, a family of new integrated barrier packaging structures developed with project partners. Solutions already available include a recyclable full PE high barrier laminate which offers a cost-effective EVOH-free solution that maximizes the amount of PE in the mono-material packaging. This satisfies tightening circular economy legislation and increases recyclability, whilst also giving a more economical high barrier packaging solution. Work is also in progress focused on developing alternative fiber-based paper packaging solutions.
4. Building a strong ecosystem of partners
It is a fact that traditional ways of working in the packaging industry are being shaken to the core, and it is increasingly clear that siloed knowledge will not lead to great progress.
BOBST embraces the value of collaborating with leading partners along the whole value chain. Several market-ready solutions have already been launched in collaboration with partners. Collaborations are carried out across technologies in BOBST Competence Centers and laboratories where new solutions are trialed, tested and validated.
5. Making Competence Centers go-to centers of excellence
The six BOBST Competence Centers are state-of-the-art facilities dedicated to flexible packaging and label technologies. They include fully equipped laboratories, pre-press rooms and equipment for personalized live streaming demonstrations, latest machine configurations, process specialists and expert operators. The Centers enable customers to assess a products technical operations and costs, and to confer with BOBST experts about their specific needs.
“In terms of new substrates and barrier functionalities, the Center in the UK offers both wet and dry coating technologies, while the LEONARDO coating line in Italy offers a multitude of coating and drying systems and can perform production scale applications,” says Sara. “LEONARDO is the only wide-web pilot line in the industry so the services that we can offer brand owners and converters are truly unique in terms of testing new packaging functionalities, as well as calculating productivity and profitability. So much so that it is fully booked for several months to come!”
Bobst Italias Competence Center also houses gravure presses and laminators that are extensively used for internal and collaborative R&D and customers trials. Joint projects are also carried out at Bobst Changzhou in China that have global resonance, as reflected by the recent award assigned by ERA (European Rotogravure Association) for press enhancement and optimized efficiency for performance with water-based inks.
CI flexo and inline flexo facilities are located in Bielefeld, Germany and Florence, Italy, respectively. Both offer an end-to-end experience from on-site plate production through to the finished reel, and are also equipped with pre-press rooms. This means faster results and a one source guarantee.
6. Making the difference with services
BOBSTs portfolio of services supports all steps of the flexible packaging production workflow, from equipment make-ready to the finished product. Digital solutions, field technicians expertise, remote services, parts and upgrades and process optimization programs, are available to increase the performance of equipment and processes.
Leadership mirrored by market performance
BOBSTs technology and market performance has secured its leadership in the area of flexible packaging.
“With the instability that has characterized the economy in the last decade, exacerbated by the COVID-19 pandemic, converters are more likely to feel confident about their future by turning to a proven, reliable business partner,” says Sara. “Our innovative offerings cover all needs and are ensuring productivity and continuity, across all technologies, for new and installed equipment. This is an important market differentiator for our customers and for us”.