Prepress
WS Display combines great customer service and flexible automation with pdfToolbox CLI
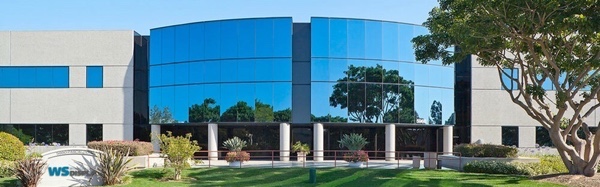
Tuesday 09. November 2021 - WS Display specializes in wholesale portable trade show displays, banner stands and large format digital printing. Founded in 2001 as initially a start-up business out of the CEOs garage in California, WS Display has transformed into an international player.
WS Display specializes in wholesale portable trade show displays, banner stands and large format digital printing. Founded in 2001 as initially a start-up business out of the CEOs garage in California, WS Display has transformed into an international player in the banner and sign market with three facilities in Carlsbad, Pennsylvania and Tijuana, Mexico serving the whole of the United States and parts of Canada.
As a wide format printer WS Display prints, sews and finishes a large variety of custom graphics ranging from umbrellas, roll up banners all the way up to 20 foot tents and custom made trade show booths.
Brian Irick, Assistant Graphic Dept Manager at WS Display: “We believe that the key to success is excellent customer service, fast turnaround times, reliability and satisfaction. As our business has grown and our capabilities have improved, our commitment to customer service and our attention to detail remains the same.”
Great customer service with flexible automation solutions
However, maintaining a commitment to customer service and fast turnaround times while growing the way WS Display has done over the last twenty years is a difficult balancing act. Because of this WS Display quickly started looking for automation solutions for its print production to avoid wasting time on repetitive jobs.
“We already had a print automation workflow system in place at WS Display, however, it had certain limitations and did not offer us the flexibility that we needed. Apart from this it was difficult to integrate with our own ERP and MIS systems. So, we wanted to create our own platform with our own software. However, we still needed reliable and flexible prepress software that could integrate with this and would be the brain around which our production would revolve. We quickly saw that pdfToolbox CLI would offer us the combination of flexibility and quality that we were looking for.”
“The main advantage is that were not doing repetitive tasks anymore. We have a lot more time to commit to the larger and more complex projects. These projects are also which are also a lot more interesting for us as a project and in which our manual intervention can really make a substantial difference in reaching customer excellence.” – Brian Irick, Assistant Graphic Dept Manager at WS Display
David van Driessche CTO at Four Pees: “You cant underestimate the complexity of certain print jobs that Brian and the people at WS Display were doing. Its one thing to print a rectangular banner and add grommet markers, its an entirely different thing if you start printing, sewing and building 20-foot tents and tradeshow booths. You need to focus on many more things than only adding bleed and cut paths.”
More than 50% of all jobs produced without manual intervention
Together with Four Pees, the design department at WS Display are looking into setting up a full CLI integration with pdfToolbox to replace their own custom-made system, which combines callas and Aleyant Tflow.
Thanks to this, the design team at WS Display can now focus more on the difficult jobs instead of manually checking all jobs. By setting up a variation of rules and checks in pdfToolbox, most of the manual and repetitive tasks are not fully automated, with over 50% of all jobs not even needing manual intervention anymore before they go to the press.
Brian Irick: “This new standalone CLI app/ui project, once launched, will fully replace our current system and be directly connected to callas and ERP therein our proof to production workflow. We hope that the current 50% of automated jobs with the current situation could reach closer to 75-80% once we finish the project.”
In the same way, pdfToolbox has helped the graphics department in optimizing media usage by analysing the designs that are delivered to the graphics department, cutting up the design in several pieces that can be nested together in the most optimal way. These pieces can then be sewn back together, creating a qualitative finished product with minimal media waste.
“The main advantage is that were not doing repetitive tasks anymore,” Irick explains. “We have a lot more time to commit to the larger and more complex projects. These projects are also which are also a lot more interesting for us as a project and in which our manual intervention can really make a substantial difference in reaching customer excellence.”
Close connections even when oceans apart
As WS Display is based in Carlsbad, California and Four Pees is based in Ghent, Belgium it would appear that coordinating such a project also had its limitations due to the distance and the time zone difference. However, nothing was further from the truth according to Irick.
“I never felt that the distance between us and Four Pees was a problem in this project,” Brian Irick explains. “Right from the kickoff meeting with David we immediately had the feeling that Four Pees truly understood what we wanted to realize with this system. It was clear they had a lot of experience in projects of this size but still knew to pinpoint those small, personalized touches to make this solution really fit our needs.”
“People often think that with these types of large projects, you need to be physically present the entire time,” David van Driessche concludes. “With this project we really proved those people wrong as we did this all remotely. The key is a good project briefing and a mutual understanding of where we wanted to go. Its a great feeling that someone on the other side of the world trusts you to do this project and that its a great end result.”