Consumables
Fakuma 2021: KURZ presents innovative and sustainable surface solutions for plastics
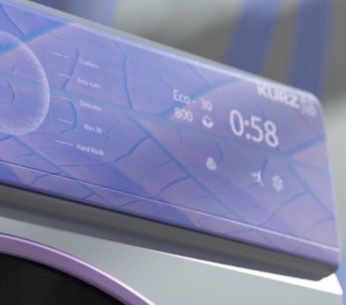
Tuesday 12. October 2021 - With the 27th Fakuma Friedrichshafen will once again become the industry meeting place for industrial plastics processing. Under the motto Making every product unique, LEONHARD KURZ will provide insights into innovative plastic surface solutions at the trade fair.
The company will be presenting itself as a “partner for future supplier challenges” with pioneering concepts, particularly in the automotive interior/exterior, consumer electronics and home appliances sectors. In addition, the thin-film expert will be focusing on its comprehensive sustainability expertise at its 120-square-metre stand number A4-4122 in Hall A4. “Fakuma is the world’s leading trade fair for all industries that have points of contact with plastics processing. We are very pleased that we will be able to present the numerous highlights that we prepared during the non-trade fair time here”, emphasises Rainer Süßmann, Head of Business Area Plastic Decoration at LEONHARD KURZ. “We will use this important platform to enable visitors to experience our comprehensive know-how in sustainable and future-oriented surface solutions. At our stand and at the stands of our partners, a wide variety of exhibits, some of them award-winning, will be on display and live demonstrations are planned. This will be complemented by in-depth information on KURZ’s sustainability expertise, which will highlight the full range of our skills.”
Automotive: solutions and components for the mobility of the future
Tomorrow’s vehicle interiors will increasingly do without mechanical switches or buttons. More and more often, the technically highly complex controls are hidden behind seamlessly closed surfaces and are only activated by touch when needed. LEONHARD KURZ is regarded as an expert in automotive interior design and will be presenting forward-looking complete solutions from the HMI (Human Machine Interface) sector at Fakuma 2021. Thanks to the efficient IMD process (In-Mold Decoration) in combination with Functional In-Mold Labelling, decoration and sensor integration can be achieved in just one process step – and thus more cost-effectively than previous processes, while at the same time offering great design freedom.
In order to give visitors to the trade fair an impression of the innovative power of LEONHARD KURZ and its subsidiaries, various demonstrators will be on show. Among other things, KURZ will be presenting an HMI concept panel at Fakuma, which only last year was honoured with the Red Dot Award for excellent product design. Furthermore, a trend-setting Concept Overhead Console, which the KURZ Group has developed in cooperation with partner companies Osram, Syntec and Wittmann Battenfeld, will be on display at the exhibition stand. In addition to a patented series-production-capable in-mould electronics solution, the headlining module also illustrates the company’s expertise in shy-tech design and ambient lighting with integrated logo projection. Live demonstrations with a Baier hybrid machine, which enables the subsequent individualisation of IMD-decorated components by means of digital printing, will be on show. The live process shows the subsequent finishing of a 3D-formed, organic component – at the trade fair in the form of an automotive door trim. IMD UNIFY also enables the combination of backlighting and shy-tech effects as well as the use of touch sensors in different integration variants, for example through functional foil bonding or functional in-mould labelling. A major advantage of the new process is the durability and excellent adhesion of the digital inks used on the surface of the injection-moulded part.
Indium as an innovative metallisation option
The presentation of new designs and real metallisations is another highlight of LEONHARD KURZ’s trade fair appearance. In addition to chrome, aluminium and tin, the company now also offers indium as a promising option: the innovative metallisation variant corresponds to the colour tone of hard chrome, but is at the same time significantly more environmentally friendly and less harmful to health than the electroplating process. Another advantage is the radar and 5G permeability of indium, which makes this metallisation option interesting for many industries: For car manufacturers, this product feature is relevant with regard to autonomous driving, for example, for exterior use on modern front panels. The same applies to manufacturers of consumer electronics who want to serve the trend towards smart consumer products with antenna technology such as mobile phones, tablets or speakers, for example. In the field of household appliances, the indium-based metallisation option also has great potential: for example, in innovative panel design and in highly functional control panels, as used in products from the smart home segment.
Automotive Exterior: KURZ sets new standards for the vehicle of tomorrow
What future trends can be expected for automotive exterior design? KURZ will also be addressing this question at its Fakuma stand. The innovative concept front panel in futuristic design, with which the company has set a milestone in the development of the vehicle of tomorrow and received the ABC Award 2020 for it, will certainly catch the eye. The groundbreaking “Iconic Space Grille” was manufactured using the particularly efficient IMD-DECOPUR process and meets all the requirements of tomorrow’s mobility: a closed, robust and self-healing polyurethane surface was created for the vehicle front, which on the one hand conveys the brand by means of logo integration and on the other hand enables visual communication of the vehicle with the environment thanks to modern and customisable backlighting effects using LED technology. In terms of design, the “Iconic Space Grille” shows the entire range of creative possibilities for the car of tomorrow: from three-dimensional depth effects to metallisation or colouring of the polyurethane layer, there are no limits to the freedom of design. Another highlight for the automotive exterior design of the future will be presented by LEONHARD KURZ together with its partner company Sumitomo Demag. At the stand of the machine manufacturer, a live production will show how a design badge in the form of a logo emblem for the front of the vehicle is created in the highly efficient “IMD second surface” process with contact-free subsequent cleaning of the component.
Home appliances: series production with highly efficient customisation
Visitors interested in the home appliances segment can also see the IMD UNIFY customisation concept for themselves. In live demonstrations, among other things, an IMD-decorated washing machine front panel will be subsequently individualised with digital printing. The special advantages of the process are the greatest possible flexibility and cost efficiency in the manufacturing process. The production of special models or regional variants is made possible in this way without additional production effort and without further transport routes. In this way, a wide variety of individualisations can be implemented for a basic décor, depending on demand and market requirements.
Consumer electronics: trend-setting product design
Possibilities for an antibacterial surface finish are becoming increasingly important – especially against the background of the Corona pandemic. The consumer electronics sector in particular includes many products that are exposed to frequent contact – for example notebooks, smartphones or even light switches. The same applies to vehicle interiors. Innovative concepts are needed here to eliminate bacteria on surfaces. LEONHARD KURZ’s answer is the IMD BIOFENSE process, which was presented for the first time last year. For this purpose, the proven In-Mold Decoration (IMD) has been supplemented by a further innovation, which guarantees an invisible antibacterial effect with a long-term effect on plastic surfaces. Trade fair visitors to Fakuma can see the advantages of the new development for themselves at the stand of the thin-film technology expert.
LEONHARD KURZ focuses on lifecycle thinking
Climate change is considered a major challenge of our time. In addition to environmentally friendly and, if possible, CO2-neutral production, energy efficiency has also become a core corporate task. KURZ meets these requirements with a comprehensive sustainability concept that makes saving resources and improving the eco-balance an important aspect of corporate management. “With our Lifecycle Thinking approach, we are committed to a holistic recycling cycle,” emphasises Johannes Romming, Manager Innovation and Sustainability at LEONHARD KURZ. “On the one hand, we ensure the recyclability of decorated components, and on the other hand, we have created a solution with RECOPOUND to produce high-quality recycling granulate from production residues. RECOPOUND is in no way inferior to virgin material in terms of the wide range of decoration possibilities, can be processed on conventional production machines and is particularly durable and robust thanks to optimised mechanical properties. The greatest advantage, however, is the protection of the environment: by using the recycled material, up to 40 percent CO2 can be saved compared to virgin material. Just how versatile and visually appealing the products made of RECOPOUND are will become clear at Fakuma. At the stand of KURZ partner Deckerform, watering cans and flower pots will be made from the recyclate as give-aways for visitors to the trade fair.