Offset Printing
Interpress Technologies – Pioneering Innovative Packaging with Heidelberg Speedmaster XL 106
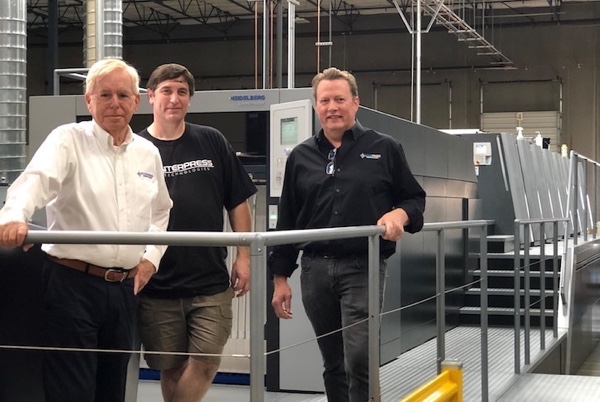
Wednesday 22. September 2021 - Interpress Technologies, Inc., with three locations nationwide, is striving to be the leader in packaging solutions. The company originally started in 1989 with old steam set presses and quickly upgraded to rotary letterpress machines.
Sheetfed offset production was then added in 2015 with the purchase of a Heidelberg Speedmaster CD 102 six-color press. The goal at that time was to bring all print production in-house for products like single-serve foods, butter, and ice-cream containers, but with much higher quality than was possible with rotary letterpress technology. After years of success with offset printing, Interpress recently installed a Speedmaster XL 106-7 with Push-to-Stop and Prinect Multicolor Toolset technology at its Sacramento, California location to keep pace with its growing customer demands.
Experimenting with Offset
In 2015, purchasing a Speedmaster CD 102 was both an investment and a bit of an experiment for Interpress. Since it was new to the technology, the company purchased a used machine to get into offset with less risk and cost but still maintain the quality and reliability of a Speedmaster. Having no prepress capabilities for offset printing, Interpress also turned to Heidelberg – installing Prinect for color management, imposition, output, and screening and a Suprasetter 106 CtP for plate imaging.
A key element of Interpresss new offset strategy was precise color control. “Shoppers buying packaged food are notoriously sensitive to color deviations,” said Rod Miner, President of Interpress Technologies. “After all, who wants to buy green oatmeal?”
For color consistency, Interpress installed Prinect Image Control, which spectrally scans the whole printed sheet and automatically balances out even the smallest deviations in the print image. “It sees color like the human eye, so it is able to differentiate even subtle shade differences in the packaging,” said Miner. Image Control detects not only all measuring elements but also solid areas using the prepress data and incorporates them into the control process. The design capability of this process control, when fully utilized, reduces costs associated with inefficiencies and helps increase productivity while still ensuring perfect color fidelity. To further the quality and consistency of its new press, Interpress decided to run its CD 102 using Heidelberg Saphira Consumables, which are all tested and optimized for maximum performance.
A Multicolor Approach
With sustained growth over four years, Interpress saw its offset production increase from one shift to three and from five-day weeks to six. Running out of capacity to keep up with customer demand and fuel growth, the company needed a new solution. Already having experience with Heidelberg technology and service, Interpress selected the Speedmaster XL 106 with Push-to-Stop technology.
According to Director of Engineering, Kevin Stephens, “We had our eye on the XL 106 for its very fast makereadies thanks to Push-to-Stop and consistent 18,000 sheets per hour production. Heidelbergs reputation for reliability and uptime were also very convincing.” The Push-to-Stop approach and the AutoPlate Pro, a fully automatic plate change system that controls precise plate feeding at the start of each job, greatly reduce the number of required operating steps during a job change. Additionally, Interpress was impressed by Prinect Inpress Control, the industry-leading inline spectrophotometer that measures and controls color and register on the fly at any speed. With Inpress Control, color fluctuations are minimized, and due to real-time monitoring, the set-up waste is greatly reduced.
Interpress was able to further reduce its waste by purchasing a seven-color XL 106. By doing so, the company has the ability to incorporate Heidelberg Prinect Multicolor Tool, which simulates true spot colors with one set of seven colors: process CMYK plus orange, green, and violet. This allows over 90% of spot colors to be reproduced in Multicolor, which eliminates a major source of downtime and solvent consumption – press wash-ups. Greatly reducing wash-ups is essential in highly regulated environments like California where solvents must be low in VOCs in order to be compliant. Another benefit of the new press is design flexibility for customers. With extended gamut, Interpresss customers are no longer limited in their high-impact graphic design or color choices that can be achieved with process colors.
An unintended benefit of Interpresss new investments has been a boost in employee morale. “These days, its hard to attract good employees, so having the most up-to-date and best technology makes us a more attractive place to work,” says Miner. “Whether it is in our die cutting area or our shipping department, we try to have the very best tools for the job.”