Offset Printing
Bobst Maintenance Plus allows full control between inspections
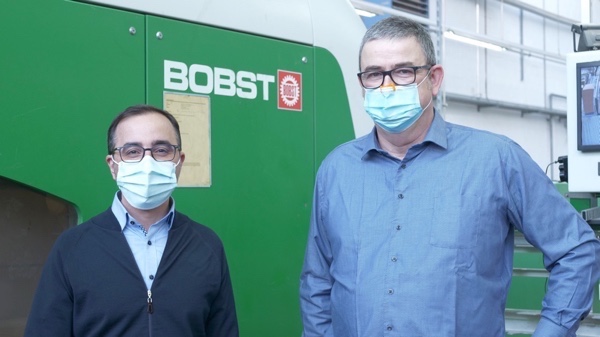
Tuesday 15. June 2021 - Despite the pandemic, SCHELLING AG is on a good course. The success of the Swiss family-owned company is based not only on the consistent expansion of capacities in growth markets, but also on intelligent inspection and maintenance solutions for its machines.
The company relies on BOBST’s Maintenance Plus service to ensure long-term production and delivery capability.
“BOBST is an important partner for us,” emphasizes Paolo Froio, he is technical manager and responsible for the availability of the machines at SCHELLING AG. Production reliability is of particular importance in the current difficult economic situation due to the Corona pandemic. “The pandemic is, of course, a special and challenging time for all of us. However, we are counting ourselves lucky, because we have withstood well at all our locations. We have a well-functioning protection concept that gives our employees a high degree of security,” explains Paolo Froio proudly. “This made the company ready to deliver at all times, which was a very important point for all our customers. Though it was disappointing, that many customers had some orders manufactured abroad, despite our government’s call for solidarity. However, some customers have come back to Switzerland because their foreign suppliers were in lockdown. They have remained to this day, which we highly appreciate.”
Packaging, a stable business area
SCHELLING AG is a family business wholly owned by the Schelling family. The company rich in tradition and whose roots date back to 1876, has over the last 25 years through mergers and acquisitions resulted in the current SCHELLING AG with six locations and around 600 employees.
“Our company history is characterized by the introduction or acquisition of ever new business areas in which we had not been active in before. SCHELLING AG has its origins in Zurich and Rupperswil in Switzerland,” explains Paolo Froio. The company in Rupperswil was and is a company in the classic corrugated board sector, producing standard and high-quality transport packaging with flexographic printing. In order to expand and grow the portfolio the company was looking for new capabilities and found them in Schafisheim, where SCHELLING AG manufactures offset laminated corrugated board. Packaging and especially displays are produced here, and it is a sector where SCHELLING AG has a leading position. The company has continued to grow with the acquisition of the location in Oensingen. “We are very strong in hot-foil and cold-foil applications. Our specialities are packaging and printed products made of solid board and paper, also with very high finishing. However, more and more combined solid board and corrugated board packaging are being produced, as SCHELLING AG has a window-patcher that can process both materials,” continues Paolo Froio.
A very big expansion step was the acquisition of Birkhäuser + GBC AG in Reinach. At this plant the company also produces commercial printing products and bags, where labels and package leaflets are particularly strong. The latter is mainly produced as packaging inserts for pharmaceuticals. “We’ve grown a lot in this field lately,” says Froio. In both Oensingen and Reinach, offset printing is mainly used. After all, the last expansion so far was not a product expansion, but a geographical expansion to Hanau near Frankfurt in Germany, an attractive market for displays.
SCHELLING AG invests heavily in new technologies. At almost all locations today, digital printing and processes in different product segments are made. In summary, Paolo Froio says: “Being broadly positioned and being able to serve basically all areas of the packaging market is the strategy and the goal that we at SCHELLING AG continue to pursue, in short “one-stop-shopping”. Our label “e3″, which stands for: economy, ecology, efficiency, underlines our strategy. From an economical, ecological and efficiency-driven perspective, we always want to offer our customers the best possible packaging solution from a single source.”
Processing and finishing with BOBST production solutions
There are, of course, various production systems and suppliers with which SCHELLING AG cooperates, but BOBST is the largest supplier in the corrugated board and folding carton sector, and SCHELLING AG is one of BOBST’s largest customers in Switzerland. In Rupperswil, for example, several BOBST presses are installed, including inline presses, flexo-printing machines and die-cutting machines, all fully automated. Also in Schafisheim and Oensingen the majority of machines come from BOBST. The tech savvy engineer enthuses when he says: “It is in our DNA, as a Swiss company we naturally consider companies that also produce in Switzerland and create jobs. This is important to us, and we hope that our customers will do the same. Accordingly, BOBST was and is an important partner for us.”
For Paolo Froio, it has always been crucial that a supplier can also deliver the solutions the company needs for increasing its productivity. For example, the Schelling Group have regularly installed beta systems in its factories, which then soon became industrial standards. “This has often been the case with BOBST in the past,” says Froio, who greatly appreciates the partnership with BOBST. “BOBST is an important partner for us because they build machines that are the most productive on the world market. In addition, the systems are very durable, of high quality and very reliable.”
Maintenance Plus being on the safe side
Since 2013, the SCHELLING Group has settled various Maintenance Plus agreements for the inspection and maintenance of its BOBST machines. Paolo Froio looks back: “I’ve been with the company for ten years now and one of the first actions was to start the Maintenance Plus program together with BOBST.” When asked “Why?” he replies: “The goal was of course, to improve the availability of our machines and, accordingly, to largely avoid or at least significantly reduce unplanned downtimes.”
According to Paolo Froio, the close partnership between SCHELLING AG and BOBST is very straightforward. For the machines that are covered by the maintenance program, a machine check takes place in a traditional way. BOBST technicians come to the company. They are specialists in flexo-printing, die-cutting or other production processes. They inspect the machine at standstill and in production. It is particularly important that the machine operators provide the technician with appropriate input if there are any special problems. This is the only way to solve them efficiently. Based on the inspection, BOBST prepares a very detailed report. It lists possible defects, such as signs of wear and tear of components. In addition, the report often also lists security-related issues, a service that Paolo Froio particularly appreciates. The report also provides recommendations for spare parts and other interventions.
The BOBST Maintenance Plus service is particularly close to the heart of the technical staff: “The good thing about this service is that we have full control all the time. In other words, we determine when we carry out certain checks. We decide whether we do it at all, whether we let our in-house technicians do the work, or it will be done by BOBST technicians. We also check which spare parts we order and which ones we already have.”
A major advantage of the Maintenance Plus service is indeed flexibility. Users benefit from full control over what they want to do at their plant. This has the great advantage that service intervals can be individually adapted to production peak times, and thus no bottlenecks arise due to inspections and maintenance work on the machines. “This was also a learning process for us,” recalls Paolo Froio, “production planning and technology have to work closely together. Of course, production should always be able to run, but we should not lose sight of the fact that maintenance work is also necessary to ensure the production reliability at all times. Maintenance is part of it, and major maintenance work cannot always happen on weekends, then we need to find time for it during weekdays.”
With an intelligent service concept as an advantage
SCHELLING AG has been relying on BOBST’s Maintenance Plus concept since 2013 and has been recording positive effects ever since. The increased availability of the machines can be measured. “There have been strong results in recent years,” Froio confirms. He continues: “We can very precisely measure the improvements by looking at our production times. We were able to increase availability by an average of 5%. In addition, the general condition of the machines is better and thus also automatically the service life of the machines is extended. Our customers are also pleased with the considerably increased quality of our products. Complaint costs have been significantly reduced in recent years. An important point is also that our operators get to know the machines better when working together with the BOBST technicians. This is a good side effect of the program. Unplanned downtimes are often very expensive, and we prevent this through the Maintenance Plus program, so that we can produce and deliver seamlessly. Of course, this also has a monetary impact.”
The entire technical team at SCHELLING is convinced of the benefits with the Maintenance Plus service, and the machine operators have been involved in the service program from the very beginning. They are obviously also interested in ensuring that their machine functions without interruption. During the machine inspection the operators can give their input and they will at the same time get to know their machine even better. In the end, it benefits the machine operators, as they will profit from improved shift performance in the form of better earnings.
Close cooperation with BOBST and future plans
When asked if he has any points that he would like to improve regarding the Maintenance Plus??????? service, Paolo Froio replies: “We are in constant contact with BOBST and that works very well. If I could express a wish, it would certainly be in the route of predictive maintenance. In other words, it would be nice if we could determine not only on the basis of analysis when a component needs to be replaced, but if it was automatically measured based on data from sensors in the machine and an early warning could be issued. But I know that there is already development ongoing in this direction and we are very excited and hopeful that we will be able to introduce this in one of our plants.”
With the Helpline Plus??????? service BOBST has the option to remotely inspect and maintain the machines. SCHELLING AG also uses this at all locations. It allows small technical errors to be corrected remotely without the need for a technician to be on site. It is a huge time saving and it leads to shorter downtimes.
For the future, SCHELLING AG intends to continue to invest in production facilities and employees. “That has always been our credo,” explains Paolo Froio. “Digital processes is a major topic. We have already invested heavily in this area, and this is what we want to push forward in the future, whether in terms of production or service. We want to continue to be an innovative partner for our customers who offer intelligent packaging solutions. As mentioned earlier always from the perspective of our label “e3”, Paolo Froio concludes.