Offset Printing
How does BOBST Connected Services strengthen Six Sigma?
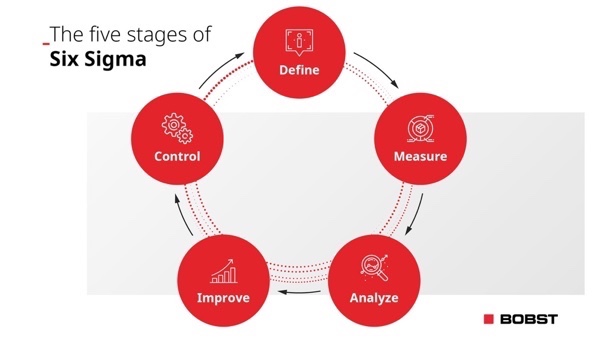
Monday 24. May 2021 - The Six Sigma methodology works with any business process and have been used by countless organizations to improve the sustainability and profitability of their operations. In this article we explore how BOBST Connected Services supports your business Six Sigma efforts.
For decades, Six Sigma has been transforming businesses. The methodology, used within a vast range of companies but most famously within manufacturing firms, allows managers to continually improve processes to increase customer satisfaction, removing the threat of defects by identifying and solving their root causes.
Six Sigma DMAIC and Connected Services
Six Sigma methods aim to eliminate production defects to six standard deviations between the process mean average and the upper and lower product specification limits. When completely implemented, this equates to just 3.4 defects per million chances of a defect – a significant efficiency saving.
One of the most common methodologies to work towards this aim is called DMAIC: Define, Measure, Analyze, Improve, and Control. This approach is typically used to improve business processes. Below, we explore how Connected Services apps benefits each Six Sigma DMAIC phase.
Define
In this stage, teams define the process to be improved and the objectives of the improvement. It requires the identification of CTQs (critical-to-quality) to ensure customer requirements are always considered.
Connect Portal, Remote Monitoring, and Downtime Tracking all benefit the Definition phase. They improve the identification of machine problems within your business processes and quantify them, allowing you to order problems by importance.
Measure
In Measure, you must create and run a data collection plan that allows you to gather accurate data on the problematic process you have defined. With this data, you can view how said process is working, and the levels of variance it exhibits.
With Connected Services apps including Remote Monitoring, Downtime Tracking, and Connect Portal, data collection is simplified. You can view and analyze both historical and live data on your machines and processes, increasing the precision of your Measure phase.
Analyze
In the Analyze phase, you must examine and identify the cause of process performance issues. Commonly, this activity gives an indication of the financial benefit of solving the problem.
Helpline Plus and Downtime Tracking are particularly useful for teams working through the Six Sigma DMAIC Analyze phase. Helpline Plus and Helpline Plus AR provide expert troubleshooting assistance for your machinery; expert advice that can help identify the root causes of machine issues. Downtime Tracking, on the other hand, provides you with analysis of machine stoppages, including Mean Time Before Failure (MTBF) and Mean Time To Repair (MTTR) reports which can help inform your analysis.
Improve
During the Improve phase, you must create lasting solutions to the problem and its root causes. Once an answer has been found, a pilot test program is launched to observe the effect and viability.
When improving the process, Connected Services apps allow you to simply track the effects of your solutions on your machinery, including ROI. All apps can be also accessed via mobile, letting your teams monitor improvements as they are first implemented on the shop floor, allowing necessary adaptations to solutions to be quickly applied.
Control
The Control phase involves precisely logging and describing the process changes that have been successfully implemented, thereby allowing the improvement to be shared with other teams. Once shared and implemented, the solution is monitored over the course of a few months to assess its long-term performance and benefit.
The data logging and analysis capabilities of Remote Monitoring, Downtime Tracking, and Connect Portal make the Control phase simpler and more efficient. Machine data can be quickly accessed and reports easily generated to support process solution monitoring, then shared with the operator to help improve machine productivity.
Six Sigma practices are an excellent way to improve product quality, customer satisfaction, and profitability, and Connected Services makes every step of the approach simpler and more effective.