Offset Printing
For 40 years, BOBST has been providing Cartonnage Lammerant with quality and reliable equipment
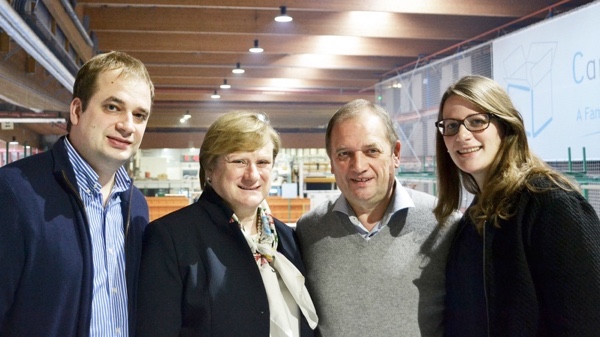
Monday 12. April 2021 - Specialized in the production of corrugated cardboard packaging, the renown company currently operates ten BOBST machines. Cartonnage Lammerant installed its fourth BOBST FFG 924 in its factory in spring 2020 in its French factory.
A Belgian family business established in 1964, Cartonnage Lammerant bought its first BOBST machine in 1981.
With 151,650 boxes produced in 8 hours, on March 8,2021 the processing company Cartonnage Lammerant attained the third highest production record on the BOBST FFG 924 machines. On the previous day, its new 6-color BOBST FFG 924 NT High Graphic (HG) machine, installed in the spring of 2020, registered 145,112 boxes, demonstrating the outstanding productivity of this line, with high-quality printing, cutting and folding of corrugated cardboard packaging in a single pass.
Folder gluer installed during the Covid-19 pandemic
As the travel restrictions during the March/April 2020 lockdown prevented Bobst Lyons Field Service Technicians (FSTs) from crossing the Belgian border, they were unable to install the folder gluer themselves on site. They solved this health-related and logistical problem with the help of Bobst Benelux, the Group’s local service entity based in Berchem (BE). Its field service technicians went to Cartonnage Lammerant to carry out the operation in its factory in Leuze-en-Hainaut, a Wallonian town about 80 km south-east of Brussels. Cartonnage Lammerant is managed by Etienne Lammerant, who was joined by his children and son-in-law between 2010 and 2018.
Working together remotely including via BOBST online services, the two teams installed the new BOBST FFG in the plant which already had three other 924 units. “This complex project has further strengthened our relationship with Lammerant” says Cyrille Tueta, Bobst Lyon Area Sales Manager. The operators, who have been working with this type of folder gluer for several years, are true partners of the BOBST technicians and have contributed to quickly commissioning the BOBST FFG 924 NT HG. “We started operating our new equipment at the beginning of May 2020 and on the second day of production, the line was already running on three shifts (3 x 8 hours)” says Mathias Lammerant, one of the managers of this Belgian family-owned company where he represents the third generation.
Versatility, flexibility and responsiveness
Specialized in corrugated food packaging, Lammerant offers a wide range of packaging solutions for fresh and frozen products. It operates in a highly competitive market, mainly in Belgium. “The challenge today is to provide a service with high added value” explains Mathias Lammerant. “Not only do we have to produce the packaging our customers want, but we must also make sure we deliver it on time (Just-In-Time) in the required quality and of course, at the best price.”?
To meet these requirements, Cartonnage Lammerant is constantly developing the versatility and flexibility of its production machinery and improving its responsiveness in fulfilling orders. For example, the processing company operates a corrugating machine in its factory that meets all its needs for cardboard. Its logistics department manages a buffer storage area of 15,000 pallets, where some of the manufactured packaging is stored to ensure deliveries to each customer according to their schedules. In just-in-time production, the volume and type of orders change every day and the schedule must be adapted on a daily basis.
“In addition to reduced production times, we also have a sharp increase in the number of product items” emphasizes Mathias Lammerant. Customers now not only manage several types of packaging, but they order boxes of different quality and complexity in continually changing quantities. With the proliferation of regulatory requirements for packaging, there are thousands of separate items.
Partner of BOBST for 40 years
The 6-color BOBST FFG 924 NT High Graphic (HG) machine provides Cartonnage Lammerant with a high-performance production line that optimally meets the requirements of its market. The automatic configuration of the Registron S5500 print register combined with the human-machine interface allows for the production of both regular slotted containers and packaging requiring complex cutting. It also ensures highly accurate printing of solid print or multicolor patterns in a single pass.
Cooperation between the two companies began in 1981 when Etienne Lammerant, the current director, bought a folder-gluer from BOBST. This machine is still in daily use in the companys factory, where ten other BOBST machines have since been installed: BOBST FFG 924, FFG 618 and FFG 1636 folder gluers, along with a BOBST DRO 1628 HBL rotary die-cutter, and more.
“With BOBST, we can cover 90% of our customers needs” says Mathias Lammerant. In a family business like Cartonnage Lammerant, the return on investments is crucial. “Every new piece of equipment we acquire is a response to market demand and the machine must be immediately operational as soon as it is commissioned” he continues. “For 40 years, BOBST has been providing us with the quality and reliability we need to succeed in our business and with high-performance production lines for high-speed orders.”?
In addition to the excellence of the manufacturers machines and the availability of BOBST services on the Belgian market, Cartonnage Lammerant also enjoys all the advantages of being loyal to the same manufacturer. Having four BOBST FFG 924 folder gluers means that the same templates and cutting tools can be used and there is a single stock of spare parts. It also means that the production schedules of operators with the same technical skills can be easily managed, as can their training on the job.
Highly automated production line
For autumn 2022, Cartonnage Lammerant has already placed a new order with Bobst Lyon. This time it has chosen the BOBST EXPERTLINE model from the FFG 8.20 range, which will also be equipped with the BOBST PREMIUM GAP CONTROL. This independent unit, placed after the FFGs counter-ejector, ensures that each delivered box is folded to customers specifications. It eliminates non-compliant packaging and optimizes the settings, reducing waste, costs and the manpower required for quality control.
With the BOBST FFG 8.20 EXPERTLINE, BOBST offers the highest-performance solution on the market. The line produces up to 24,000 boxes per hour and is capable of producing both regular slotted containers and complex corrugated cardboard packaging.
Such speed and quality of production are achieved by means of the high degree of automation and connectivity of the line. The BOBST FFG 8.20 EXPERTLINE has a continuous cardboard feed at nominal speed that does not require any operator intervention. This also applies for feeding the first sheets of each order. The upstream parts of the line are configured automatically before completion of the current order. This technological achievement results from the Sequential Order Change (SOC) system fitted to the machine, which ensures very fast set-up times of only one to two minutes. The level of automation achieved by the BOBST FFG 8.20 EXPERTLINE means the entire production line can be run by only two operators.
With this equipment, the Cartonnage Lammerant integrated company will have a high-performance production tool designed for all types of high-speed orders