Consumables
Baldwin receives three FlexoCleanerBrushTM orders in 30 days
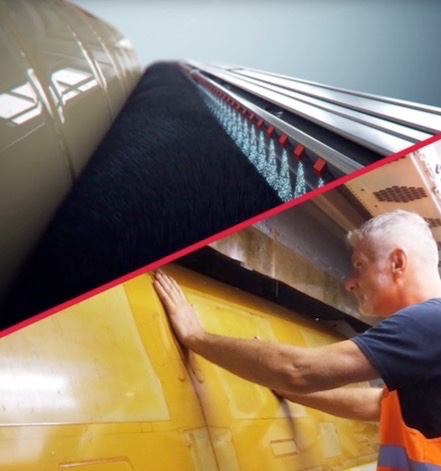
Monday 29. March 2021 - During the COVID-19 pandemic, Baldwin has delivered a total of 30 FlexoCleanerBrush cleaning heads, thanks to close collaboration between onsite team members, local agents, the companys global sales organization,and support from its product and technology center in Germany.
Baldwin Technology Company Inc. has successfully landed three new FlexoCleanerBrush orders, with a total of 16 cleaning heads, from customers in the US and Germany.
With the FlexoCleanerBrush system, an inline cleaning station installed within each print unit uses a brush that runs the full width of each printing plate. Paired with a precision spray application system, the FlexoCleanerBrush evenly distributes a mixture of detergent and water across the plate as it spins, gently cleaning its surface. The plates are then dried by the integrated air knife.
“With two of the recent orders, the customers had already installed the FlexoCleanerBrush in other locations. One of them reported as much as a 30 percent production capacity increase, thanks to the installation,” said Lee Simmonds, Regional Sales Manager at Baldwin. “Both customers have experienced insufficient results with their original traversing cloth cleaning systems, which will now be removed and replaced with the full-width, stand-alone, automated FlexoCleanerBrush technology from Baldwin.”
Improving sustainability is one of the key drivers for investments in the corrugated printing industry. The FlexoCleanerBrush dramatically cuts water waste by cleaning plates more efficiently. In a recent independent study that was conducted to validate the capacity of the automated system, the FlexoCleanerBrush could fully clean and dry all printing plates in less than four minutes and pick hickeys in seconds.
Besides offering efficient cleaning during runs and fast end-of-job cleaning, the FlexoCleanerBrush system also enables operators to remove dryplatesfrom the machine without the potential riskof plates sticking together once they are placed back in the plate- racking system. This helps to ensure increased board throughput, less downtime and a safer working environment by eliminating operators contact with nip points, moving parts and chemicals.