Finishing & Screen Printing
BOBST ultimate MASTERFOLD 75110 folder-gluer pushes the boundaries of productivity
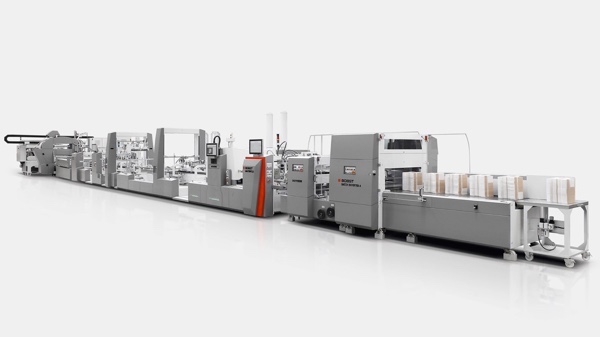
Wednesday 24. March 2021 - Incorporating new BOBST branding, the MASTERFOLD 75110 maintains its unrivalled status as the fastest, most automated folding-gluing line available today. With very short make-ready times, the folder-gluer delivers efficient and reliable non-stop production of outstanding quality products.
Pierre Binggeli, Product Line Director Folder-gluers at BOBST, said: “BOBST has identified four cornerstones crucial to the future of packaging production; namely sustainability, automation, connectivity and digitalization. Our vision is anchored in data access and control across the entire workflow to support customers achieve greater flexibility, agility and efficiency.
“With the BOBST MASTERFOLD 75/110, packaging converters can reap the benefits that automation brings. Enabling more to be achieved with less, automation brings greater productivity, throughput and sustainability to the production line, optimizing both people and machine performance without compromising on quality and accuracy. With highly automated machines, like the MASTERFOLD, packaging manufacturers have the opportunity to adapt quickly to shifts in the market and periods of peak demand and pressure, like those we have seen over the past 12 months, while maintaining a high degree of efficiency.”
Equipped with a series of automated setting functions, the BOBST MASTERFOLD 75/110 enables very short make-ready times and supports non-stop production, able to produce up to 2.7 million perfectly executed boxes per day. It is proof that converters can achieve greater productivity without compromising on efficiency and quality. Also, the folder-gluer is designed with open frames and platforms, which increases the operators ergonomics and simplifies changeovers. With its new makeover, the cost of ownership is decreased, maintenance is simplified, and the machines accessibility is further increased.
The performance of the MASTERFOLD in terms of productivity, ergonomics and user-friendliness is also enhanced by a range of dedicated devices and peripherals.
Complementary peripherals create a fully automated, high performance folding-gluing line. The EASYFEEDER / BATCH INVERTER 4 motorized pre-feeder allows consistent and smooth feeding of blanks, preventing unscheduled production stops and further increasing productivity. The CARTONPACK 4 high performance packer automatically fills shipping containers with folded and glued cartons. It can also work in conjunction with CASE ERECTOR, which automatically erects the containers to be filled. Thanks to these peripherals, the reduction in manual workload also improves the working conditions for the operator and will help avoid issues with repetitive strain injury and other work-related health problems.
In response to e-commerce growth in 2020, the GYROBOX complementary device is a key solution to producing folding carton e-commerce boxes, faster and more efficiently. This device simplifies the production of complex boxes by rotating blanks in line between two folding processes. Thus, it allows the rapid folding-gluing of boxes in a single pass – speeding up the production process, boosting efficiency and delivering an exceptional quality finished product.
Mr. Binggeli added: “And lets not forget the ACCUCHECK quality control solution, which inspects every carton, filters and ejects automatically defectives ones, guaranteeing 100% quality-controlled production. In short, the ACCUCHECK enables converters to increase efficiency and reduce waste with the aim of delivering zero-fault packaging to their clients.
“BOBST is committed to providing the technologies, innovation and capabilities to packaging converters that enable them to be agile and responsive to the needs of retailers and brands in a dynamic, evolving economy. The MASTERFOLD 75/110 is a perfect demonstration of this in practice.”