Offset Printing
NORTIERs printed packaging demands high quality production: BOBSTs new ACCUCHECK provides the answer
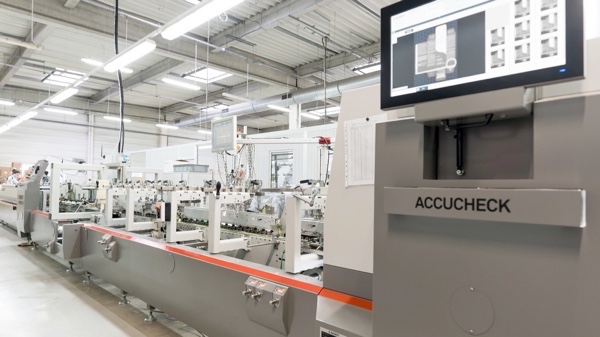
Monday 15. March 2021 - NORTIER, located near Paris, has been a major player in offset printing and the development of high-end compact cardboard packaging since 1905. The company specializes in the luxury sector, particularly cosmetics, perfumes and spirits.
Removing faults in packaging production is important for all industries. But for some – such as pharmaceuticals and high-end luxury packaging – it is absolutely essential.
“Because we specialize in high-end packaging, we use a lot of different processes in our packaging production lines, mainly offset or digital printing, varnishing or laminating, hot stamping, embossing, cutting and folding-gluing,” said Didier Rochas, President of NORTIER. “These cumulative processes increase the risk of defects in the production line, and errors in our industry can be very costly.”
Because of this, the company was an early adopter of the first generation of the ACCUCHECK from BOBST. The company invested in two ACCUCHECK devices in 2012 to identify defects in its folder-gluer lines. At the time, ACCUCHECK was the world’s first built-in zero-fault quality control device for folding and gluing machines.
“The high-performance and fully integrated solution, which was more intended for the pharmaceutical industry, appealed to us,” explained Mr. Rochas. “The technology had an impressive detection capability on value-added surfaces without affecting our production speed. This was a tremendous competitive advantage.”
After the introduction of the first generation ACCUCHECK, BOBST has continued to innovate and has recently launched the new ACCUCHECK, which makes zero-fault packaging a reality.
The new ACCUCHECK is an in-line solution to inspect carton blanks for defects as they enter the BOBST folder-gluer and is compatible with the latest generation of BOBST MASTERFOLD 75|110 or BOBST EXPERTFOLD 50|80|110 machines. The in-line solution is fully embedded into the folding-gluing line, allowing a seamless progression, with no additional quality control step in the process required. As a result, production quality processes are improved while quality check running costs are reduced.
As with the first generation, the new ACCUCHECK carefully checks carton blanks for defects and guarantees complete quality consistency, but now at a considerably faster speed – up to 500m per minute, or 140,000 boxes an hour. In addition, the system detects a wide range of defects, including spots, missing prints, text errors or misregistration. Defective boxes are then filtered and ejected automatically, guaranteeing 100% quality-controlled production.
Other new features include advanced reporting, PDF functions and the new Smart Text Inspection feature, which ensures that even the smallest defects like non-compliant words or numbers are detected. BOBST has also introduced dedicated inspections for embossed, metallized and varnished surfaces, which are very useful features for producers of high-end luxury packaging such as NORTIER.
The folding-gluing line is also easy to use. The new ACCUCHECK is equipped with the HMI SPHERE, which provides several operating modes for customized setting and easy operation. This feature is becoming standard on new BOBST machines. In addition, inspection parameters can be saved and recalled, with repeat orders set within seconds. Access rights can be set for different users.
Pierre Binggeli, Product Line Director Folder-gluers at BOBST, commented: “BOBST was the first folder-gluer manufacturer to offer this kind of quality control device. With the new ACCUCHECK, we have taken automated quality control to the next level. We have a completely integrated solution, which is unique in the industry. The new ACCUCHECK can be configured to suit all industry segments, with different speeds and inspection needs that serve other industries just as well as the cosmetic one.”
A strong partnership between BOBST and NORTIER
“Achieving zero-fault packaging is a key goal for all our customers,” said Claude Tomà, Technology Sales Manager for Folder-gluers at BOBST. “They want to ensure perfect quality production and timely detection of any errors within the production chain. They need a system they can rely on to identify issues and eliminate sources of errors, leading to quality consistency and client satisfaction.”
As a trusted long-term partner, NORTIER was selected as a “beta” site for the development of the new ACCUCHECK, and collaborations like this were invaluable in helping to refine the device to perfectly suit the needs of BOBSTs customers.
“We had specific needs and we wanted to work with the BOBST specialists in order to develop the technology further,” said Mr. Rochas. “Our requests and exchanges with BOBST have helped to shape the new features that are present today. This result was achieved thanks to the excellent cooperation between all the teams because the objectives we had set ourselves at the beginning were very high.
Today, our teams have in its hands a powerful tool that allows us to deliver 100%-controlled packaging. All of this without impacting our production speed. In fact, the new ACCUCHECK has increased our efficiency and agility.”
Mr. Tomà added: “We are grateful to NORTIER for their loyalty toward BOBST. As business partners we always aim to deliver the highest quality in both equipment and service. The new ACCUCHECK is the outcome of our precious collaboration.”
New ACCUCHECK helps to bring BOBSTs vision to life
The device exemplifies BOBSTs vision to shape the future of the packaging world. Based on four key pillars – connectivity, digitalization, automation and sustainability – the Group vision is to connect customers to a digitalized and automated workflow, while at the same time providing best-in class machines and a great service experience.
At the heart of BOBSTs vision is BOBST CONNECT, an open architecture cloud-based platform that will help to orchestrate the production process from the clients PDF to the finished product, via the four key pillars.
Mr. Binggeli concluded: “The new ACCUCHECK is one strategic element within BOBST Connect. It enables increases in efficiency and reduces waste with the aim of delivering zero-fault packaging to the satisfaction of the converters and brand owners.”