Finishing & Screen Printing
Mediahaus increases productivity with BOBST die-cutting and tooling solutions
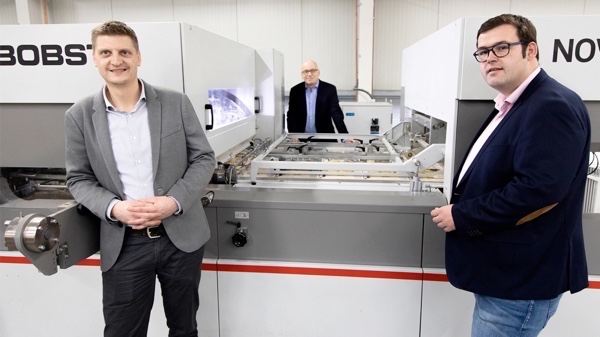
Monday 08. March 2021 - Why German packaging manufacturer and service provider Mediahaus trusts BOBST to optimize its processes in folding carton production. For almost two decades, Mediahaus has continued to expand its Packaging Solutions division through large investments in the latest technology.
The commissioning of a new BOBST NOVACUT 106 E flatbed die-cutter and a fully automatic CARTONPACK 4 packaging system at the beginning of 2020 marks a new high point in this collaboration. The company has been partnering with BOBST for folding carton production since 2014.
The philosophy of Mediahaus Walfort GmbH could hardly fit better with the future vision of the Bobst Group, in which digitalization, connectivity, automation and sustainability form the cornerstones of a new reality in packaging production. “We see digitalization as a source of opportunity – both for our company and for our customers. Wherever possible we digitalize, connect and automate our processes,” explained Managing Director Jan Hendrik Walfort.
High quality tooling is key
The BOBST NOVACUT 106 E flatbed die-cutter and the fully automatic CARTONPACK 4 packaging system were part of an investment package worth 4.5 million for 2020 alone. “In the production of high-end packaging, the die-cutting process plays a key role,” noted Mr Walfort. “We wanted to reposition ourselves and the BOBST NOVACUT 106 E met our requirements with an attractive price-performance ratio.” Before meeting with machine manufacturers, the Mediahaus team had prepared full specifications that defined its requirements in terms of productivity, flexibility and quality.
For tooling, Mediahaus turned to Jeurink Stanzformtechnik in Neuenhaus, a BOBST technology partner. In view of its broad portfolio, Mediahaus requires a number of different cutting dies. “Jeurink knows the requirements of the BOBST NOVACUT 106 E well and takes them into account when building our tools. That enables us to make full use of the high hourly output of the BOBST NOVACUT 106 E of up to 8,000 sheets per hour,” said Print Shop Manager Marco Segeler.
BOBST tooling solutions is geared towards enabling customers to achieve maximum productivity, quality and profitability in the die-cutting process. The supporting measures range from advising customers to training courses for machine operators and certification of selected die manufacturers.
Ease of use and higher output
One major benefit of the new investment has been moving from three shifts down to two. “Thanks to the machines higher output and shorter change-over times, we now work in two shifts and keep the third in reserve for future growth,” said Mr Walfort. “We expected to be 30% faster in set-up compared to our previous machine, and we are well on our way there.” Each shift usually produces three to five jobs.
The ease of use in change-over has resulted in higher productivity and freed up the BOBST NOVACUT 106 E for more work. The operator is guided step-by-step through the intuitive set-up process on a full colour 22-inch HMI, and the high level of automation features makes job changes much easier and faster. These include the integrated Quick-Lock system, the automatic locking and unlocking of the upper stripping tools and the CENTERLINE system for assembling, positioning and centering the tools.
From the packaging manufacturers point of view, the feeder and the automatic non-stop delivery of the BOBST NOVACUT 106 E have been thought through down to the last detail. Stack changes are also done automatically. “With production speeds of up to 8,000 sheets per hour, there is simply no time for manual intervention in the delivery,” noted Mr Segeler.
With the number of smaller orders increasing, the optimization of set-up times has become even more important.
Mr Walfort said, “Regardless of whether the orders are large or small – we have to produce them as quickly and profitably as possible. Our new technology has enabled us to make a leap in performance and quality, and it supports the flexibility for which our owner-managed, medium-sized company is known in the market. In an emergency, we can produce a job in just a few days.”
Exploit potential benefits
In order to be able to exploit the synergies of its new technology in the pressroom and in folding carton production fully, Mediahaus took a holistic approach to the analysis of its production processes.
“Before making our decision, we carefully compared the performance features of the technology and watched the machines in operation,” explained Mr Walfort. “BOBST is known for its very good machines, and we know from our experience with our folder-gluer that its technology and services are reliable. Otherwise, we simply couldnt rely on just one die-cutter,” he concluded.
As well as reaping the benefits of the new investments, Mediahaus also enjoys the Maintenance Plus service offering from BOBST for regular preventive maintenance, and with BOBST supporting the company for full process optimization, there will be more opportunities to increase productivity in the future.
In 2008, MEDIAHAUS Walfort GmbH, based in Ahaus not far from the border with the Netherlands, was a commercial printing company. Today the family company, which was founded in 1978 and employs more than 150 staff, generates over 80% of its sales through high-quality packaging for a very diverse range of customers. The operational business of the innovative media service provider is divided into two service areas: Media Solutions and Packaging Solutions, so customers have only one point of contact for all aspects of their media production.