Offset Printing
Think green by increasing output by 50 per cent and halving makeready time
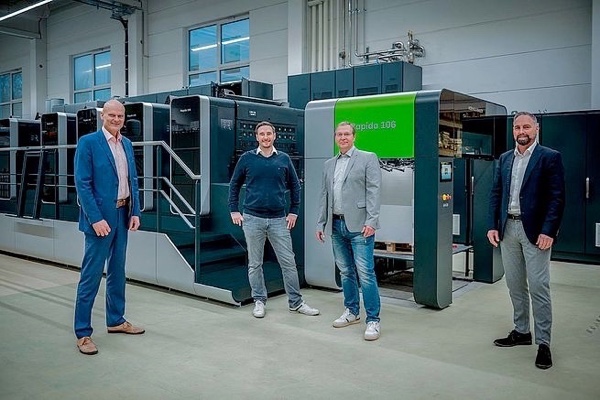
Thursday 11. February 2021 - The ARNOLD group, which is based in Großbeeren near Berlin, treated itself to a very special Christmas present at the end of last year. 23 December marked the start of production on a brand new Rapida 106 X from Koenig & Bauer.
Right from the very first day, the eight-colour press with perfecting unit and an additional coater boosted output by 50 per cent and enabled makeready times to be slashed by half. Max Arnold, managing director of the highly technophile commercial printing company, is delighted: “Whenever I come into the press hall, I see the bright red number 18,000.” And it is not only in terms of speed, but also in regard to its technical features, that the Rapida 106 X meets all the demands of modern, efficient and future-oriented print production.
Alongside its printing facility, the ARNOLD group also operates a pre-press studio and an advertising agency, and all three conduct intensive reviews of each and every process from the perspectives of ecology and sustainability. “Think green” is not just a slogan, but also the company’s guiding principle. Process-free plates are used, with production being based solely on alcohol-free printing with mineral-oil-free bio-inks, and green electricity from the companys own photovoltaic installation contributes to an outstanding ecological footprint.
Ecological production processes in the foreground
The Rapida 106 X perfectly complements this approach. After all, it handles production processes that would otherwise require two presses. 4/4-colour print products are completed in a single pass, including any necessary coating refinements. The convertible perfecting unit also makes it possible to print using more than four colours in straight production, for example for packaging. The power consumed by one such press is, of course, lower than two presses, while countless special features allow the ARNOLD group to benefit from ecological print processes, and to reduce waste to an absolute minimum.
Foremost on the list is QualiTronic PDFCheck, which complements colour control by incorporating sheet inspection functions and a comparison with the PDF from pre-press. Checking every single sheet lowers the level of waste significantly. Documentation of the print quality and the marking of any waste sheets in a pile by using a tag inserter are also attractive propositions for particularly quality-sensitive customers. Furthermore, the short, fast-reacting inking units bring the press into colour in next to no time, which makes a similarly decisive contribution to minimising waste.
Ecological production and high quality print products are by no means mutually exclusive. On the contrary, every print job that the ARNOLD group completes demonstrates once again that high product quality can also be achieved while observing strict ecological criteria.
First Rapida press at the company
The new press is the first purchase from Koenig & Bauer since the company was founded in 1989. Alongside the ecological aspects, there were several other factors which clinched the deal: the reputation for flexibility and collaborative support provided by industry system house Steuber, the companys longstanding partner for service and post-press equipment, the relative proximity of the manufacturing plant in Radebeul, the potential of key technical features, and the design of the Rapida 106 X series.
Production manager Felix Berndt is especially impressed by the feeder, the sidelay-free infeed and the delivery of the press: “You push the pallets in and the press simply gobbles up everything with ease,” is how he describes his first experiences of production with a diverse range of substrates. And on top of that, “the pile in the delivery is sometimes even tidier than the one in the feeder”. Foil-free ink ducts, with a special coating to enable fast ink changes, simplify handling. The Duraprint rollers in the inking units exhibit excellent dimensional stability and are not subject to wear. Job changeover times have been shortened several times over thanks to the fast plate changes and optimised washing processes with CleanTronic Synchro.
Ongoing optimisation of the production process
There are times when even a single centimetre makes all the difference: increasing the format expansion from 74 to 75 × 105 cm means that a standard paper size is suitable for use on the Rapida 106 X. Ordering expensive special formats, trimming the unwanted centimetre or printing with smaller sheets, as was the case with the predecessor press, is no longer necessary, making the entire process more efficient. The larger sheet format can be better utilised.
“Every investment helps transform and optimise processes,” says Max Arnold. Together with his father and company founder Andreas Arnold, he viewed installation of the Rapida 106 X as an opportunity to streamline the logistics concept used in the press hall. The significant increase in productivity at the printing stage does, of course, affect capacities elsewhere in the company. Accordingly, the management is now working on attracting new customers so that it can utilise the full capacity of the Rapida 106 X and keep the two-and-a-half daily shifts busy.
A motivated team
The printers are just as excited as their managers. “The press found immediate acceptance, and they are really impressed,” Max Arnold reports.
The first quarter of last year was the most successful in the history of the ARNOLD group. That convinced the family owners that it was the right time to invest, despite the coronavirus pandemic. Almost a year later, Andreas and Max Arnold are looking to the future with optimism. The next step in their plans is to modernise the storage and logistics facilities. At the same time, they are very interested in an MIS system in combination with a fully integrated tracking app.
The ARNOLD group’s commitment to the environment:
Use of sustainable substrates (FSC-certified or Blue Angel)
Exclusive use of process-free printing plates (reduced consumption of chemicals, water and energy)
Alcohol-free printing with eco-friendly and particularly sustainable inks
Use of coatings with a Blue Angel certification
Carbon-neutral printing
Use of green power (avoiding between 155 and 175 tonnes of CO2 emissions each year)
Tree donations for Berlin and the state of Brandenburg
Use of an electric or hybrid vehicle fleet