Prepress
Printing House Merkur Digitizes Customer Service and Production with Keyline
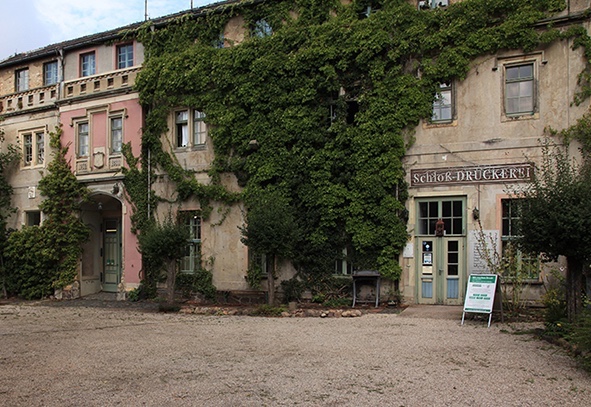
Monday 08. February 2021 - Time is money - this is more true than ever in the printing industry. Today, the margin no longer comes from production, but from optimal processes. Merkur Druck & Kopierzentrum in Leipzig (Germany) understood this a while ago. After digitizing the processes with the Keyline print business management software, everything runs more efficiently and smoothly.
The family business, which has been in existence for 30 years and is named after the Greek god of merchants and thieves, has its headquarters in Schloss Püchau near Leipzig. There and in two branches in Leipzig, 22 employees ensure the steady growth of the company. René Huhn, managing director of Merkur Druck together with his brother André and owner Hans Huhn: “We produce almost everything that is possible on paper and also on other materials”.
At Merkur Druck, too, the trend is clearly towards digital printing, especially in direct marketing and lettershop. In the area of print finishing, digital foil stamping and die cutting as well as high-power laser cutting of various materials are offered, among other things.
Costing was a bottleneck
Merkur Druck has always invested in digital technology in production and finishing. For many years, however, calculations were still based on price lists that were updated every few years, as is the case in so many other print businesses. It could take several hours to create a quotation, and if there were any changes to the order, the process had to start all over again.
In today’s printing industry, this is no longer acceptable. Many small jobs have to be completed as quickly and cost-effectively as possible under high time pressure. René and André Huhn took the upcoming company succession in the family business as an opportunity to rethink the processes.
Savings potential only through process optimization
René Huhn comments: “There is hardly any savings potential in the costs for paper and ink; they are unlikely to drop. The money today comes from the consistent optimization of processes and the entire workflow in and between all areas. This was not consistently possible with the previous Excel-based solution. When a costly upgrade became necessary for this, we started looking for alternatives.”
Several systems in the choice
The company was looking for a solution that could map all stages of the value chain, from costing to shipping. The Merkur Druck team looked at a whole range of classic MIS applications for print shops. However, many systems did not cover all areas, or they were too inflexible and complex. Some worked strictly on an article basis: A separate article number had to be created for each part product – they usually ignored the production time with the effective personnel costs for this.
A clear advantage as a cloud application
In addition, most of the solutions had to be installed locally. Since Merkur Druck operates two branches in addition to its headquarters, these would have had to be connected with some technical effort. Cloud-based software such as Keyline, which can be used from any location via the browser, has a clear advantage here.
Keyline was able to score during the test phase already. René Huhn: “Since Keyline is offered in the Software-as-a-Service model, the complete scope of functions is instantly available via the test access. I got to grips with it over a weekend.”
Always in the know about all jobs
Today, Merkur Druck’s customer service and production processes run smoothly and with high efficiency across all locations. Quoting is usually completed in minutes. The fully automated production planning takes into account delivery times, priorities, material availability, capacities, setup costs and much more.
Even in the event of changes, the digital job folder always summarizes all production-relevant information for each job in an up-to-date manner. The production board provides real-time information on the status of the job from various perspectives, such as resource utilization and order and product status – a plus also in communication with customers.
Important assets: Flexibility and openness
René Huhn also appreciates Keyline’s flexibility and openness: “In Keyline, we can specify everything ourselves according to our requirements, including our own formulas. Thanks to the simple transfer of data from Keyline to the leading German tax software, the team also saves an enormous amount of time in accounting.”
Great support from a reliable partner
René Huhn emphasizes that the team never felt left alone during the implementation of Keyline: “We were already worried whether we would be able to manage the changeover. But the support by phone and chat gave us a good helping hand and always reacted quickly when we had questions. We also feel safe in our decision because the Keyline developer Zaikio is part of the Heidelberg family.”
Being there from the start
By opting for Keyline, Merkur Druck has its finger on the pulse of digitization in the printing industry. René Huhn: “Zaikio is developing a very interesting approach to the digital transformation of print businesses with its platform of the same name – and we wanted to be part of that movement from the very beginning. Using state-of-the-art technologies, the Zaikio platform brings together print businesses, customers, brand owners, suppliers, and software and machine manufacturers so that everyone can communicate and exchange data at eye level.