Offset Printing
An FFG 8.20 BS EXPERTLINE inline machine from BOBST at Wellkistenfabrik Fritz Peters
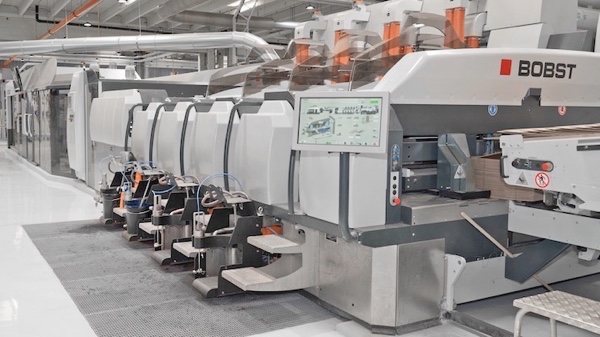
Thursday 07. January 2021 - Around nine years ago, Wellkistenfabrik Fritz Peters GmbH & Co. KG in Moers, Germany, started along the road to full optimization of their production processes, which significantly increased productivity and flexibility.
With the BOBST FFG 8.20 BS EXPERTLINE inline machine, which commenced operation in February 2020, the packaging manufacturer further strengthened its market position.
“Today our customers involve us closely in their package development. Weve worked toward this in recent years,” explains Winfried Flemmer, CEO. “Back in 2012 we thought, let’s do away with cookie-cutter products and the price wars that so many competitors have to deal with!”
Together, Mr Flemmer and the current operations manager Jonas Grundmann, developed a strategy for total process optimization. Automation and productivity were to increase significantly. Machine downtime and production bottlenecks, especially at peak times, were to be eliminated. Investments in the latest technology were aimed at freeing up shifts for additional jobs.
“The next logical step was expanding our capacity in the inline area,” recalls Grundmann, naming one of the main reasons why a Bobst FFG 8.20 BS EXPERTLINE beat the competition. “With this automatic inline machine, we now produce jobs in one step that would have required two work stages in the past.”
Moreover, in production of premium folding boxes, the machine offers the flexibility that packaging manufacturers need to meet the markets latest demands. “The FFG 8.20 BS EXPERTLINE reliably processes double-walled grades, such as BC flute, it produces packages with tuck-in bottoms and prints uniquely well-coordinated complete surfaces with high register accuracy,” says Grundmann of some of the new possibilities the company now uses to generate additional revenue. The high-production inline machine covers a broad spectrum: It processes corrugated board 1.2 mm to 8 mm thick, and sheet sizes from 250 mm x 625 mm to 1,050 mm x 2,180 mm. The maximum print width is 2,000 mm.
The FFG 8.20 BS EXPERTLINE at Wellkistenfabrik Fritz Peters is equipped with four presses and hot-air dryers. This dryer enables the machine to produce folding boxes with large full-surface printing in less time, at speeds up to 18,000 sheets an hour, making for very high productivity. According to Grundmann, “With packaging that doesn’t have to be pressed, the FFG 8.20 BS EXPERTLINE actually gives us a maximum speed of 24,000 sheets per hour. This machine is made to go full throttle,” he says.
Designed for high-quality production
Installation was planned and carefully prepared in close cooperation with BOBST. This means that the inline machine stands on a solid foundation that absorbs any vibration. It forms the basis both for high print quality and for very precise folding and gluing. “Sheet transport is very well designed on the FFG 8.20 BS EXPERTLINE. It eliminates fluctuations, which is why the machine produces folding boxes with exact gap widths. We always specify a gap width of 8 mm and maintain it on the machine at a tolerance no greater than ± 2 mm,” says Grundmann.
The high precision in sheet transport begins with a DFB (direct feed belt) inserter that works without feed rollers. It feeds the sheet directly to the printers vacuum transport. Even with light sheets, it eliminates any calibration losses, so the packages have better characteristics. For Wellkistenfabrik, another highlight is the fluid folding device in the slotter. It sprays a small amount of water on the parts of the packages where folds are made. “The moistening makes the folds more precise. We mainly turn this option on with double-wall, such as BC and EB,” Grundmann reports. The calibration section in the folder-gluer also helps ensure high-quality folded boxes by perfectly aligning the folded sheets, again improving the dimensional accuracy of the completed packaging. “So far, weve never had a complaint about the FFG 8.20 BS EXPERTLINE,” says Flemmer, stressing that the folding boxes work perfectly in customers automatic filling machines.
Automation allows fast job changes
Developed on a new platform, the inline machine stands out for its extremely simple, intuitive operation. This is evident in the very short setup times. Most jobs that run in Moers are between 5,000 m² and 15,000 m². This means quite a few job changes per shift. “During yesterdays morning shift, we sent 16 jobs through the FFG 8.20 BS EXPERTLINE, and 11 jobs on the afternoon shift,” says Grundmann. These days, the machine is usually run for two shifts. This means the plant has reserve capacity, so it can take more orders for premium folded boxes.
The FFG 8.20 BS EXPERTLINE is connected to BOBSTs Remote Service Helpline Plus. The machine manufacturers technicians can dial into the machine controls, analyze the process, and in most cases fix malfunctions online. “The BOBST Services team is very committed and well qualified. We also have to thank the BOBST instructors very efficient training, which enabled efficient commissioning,” Grundmann says. “We made the right investment decision.”