Offset Printing
Ever more customers opt for Heidelberg subscription packages
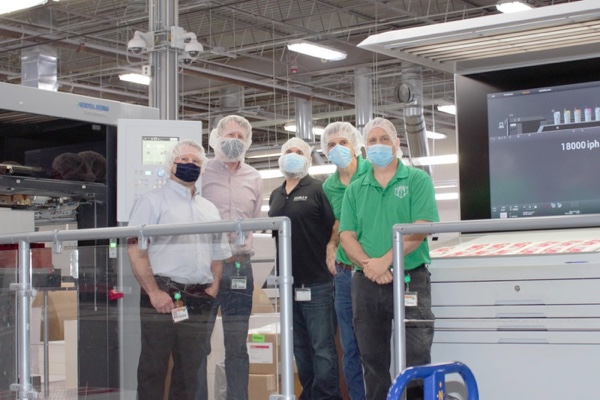
Monday 07. December 2020 - By opting for one of the new data-based packages on offer from Heidelberger Druckmaschinen AG (Heidelberg), an increasing number of print shops worldwide are benefiting from the variable options of these Print Site Contracts. Customers have a choice of four packages with different scopes of services and methods of payment.
They range from a “Lifecycle Smart” contract that includes services and consumables to a “Subscription Plus” package that covers consulting, training, service, consumables, Prinect software, and equipment solutions. All four packages aim to maximize customers overall equipment efficiency (OEE), which delivers genuine added value compared to purchasing individual components. Heidelberg has now concluded some 400 of these contracts across the entire range, and they already account for over ten percent of the companys total sales.
U.S. print shop Old York Road Printing sees successful results with Heidelberg Subscription
Based in Warminster, in the United States, Old York Road Printing (OYRP) decided on a Heidelberg Subscription agreement for its food packaging division. Covering one of the companys latest-generation Speedmaster XL 106 presses with Push to Stop technology, the subscription contract also includes Prinect software, Saphira consumables, spare parts, consulting, and service operations. Billing is based on the number of sheets printed.
Working together, Heidelberg and OYRP use existing data to analyze and optimize operating processes while also further reducing production costs. Within four months of commissioning the new system, this has significantly increased the print output. All key performance indicators have improved, with less makeready time, less waste, and a higher job throughout.
The machine produces up to 90 print jobs in 24 hours and always operates at the maximum speed of 18,000 sheets per hour. Makeready times between jobs are no more than around five minutes. “When we defined our targets at the outset, I never thought the XL 106 would be able to handle this volume, but the new press is exceeding all our expectations,” says OYRP Plant Manager Tom Chwieroth.
Lifecycle Smart contract means fewer interfaces and enhanced productivity for Hoehl-Druck Medien + Service GmbH
Hoehl-Druck Medien + Service GmbH (Hoehl-Druck) is based in the German town of Bad Hersfeld and has a printing tradition dating back over 250 years. Its services are now aimed at a variety of customers from the commercial printing sector and the pharmaceuticals industry. The company is committed to strong, reliable partnerships with its customers and suppliers, which is why it decided on a comprehensive package from Heidelberg. The Lifecycle Smart contract it has entered into covers all service operations for a Speedmaster SX 102 with Image Control and a Speedmaster CX 102, together with virtually all necessary consumables for a period of two years. All the rest of the companys Heidelberg systems benefit from Remote Service as a minimum. The total contract value is in the mid six-digit euro range.
“Reliable partnerships are extremely important to us if we are to maintain our high quality and give our customers in the pharmaceuticals, cosmetics, and food industries everything they need for their highly sensitive products,” underlines Hoehl-Drucks Managing Director Markus Gutberlet. “Thats why the Heidelberg contract model won us over. Having just one contact for a large number of matters helps us eliminate numerous interfaces. Knowing Heidelberg is ensuring the availability of all systems means we can focus our full attention on the needs of our customers,” he adds.
“Partnerships based on digitization are paying dividends – for our customers and for Heidelberg itself. More and more print shops are opting for our Print Site Contracts,” says Heidelberg CEO Rainer Hundsdörfer. “Their variability is the main advantage, with customers choosing the option that best suits their needs. Production processes have improved and productivity has increased in virtually every single case. By analyzing our wealth of data, we know exactly where our customers are experiencing problems and precisely which optimization steps we need to initiate together,” he concludes.