Consumables
Defender – new inspection and defect tracking solution from Baldwin Vision Systems
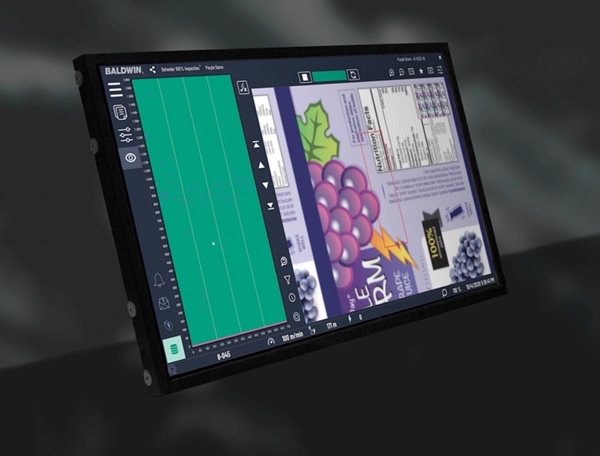
Monday 02. November 2020 - Baldwin Vision Systems is introducing Defender, a new data networked technology package for detecting, tracking and correcting printing errors. Designed specifically for wide web packaging substrates, Defender 100% Inspection is the foundation for the industrys most comprehensive defect tracking solution. Defender Data Central and Defender Waste Manager together form a seamless workflow for defect detection and tracking.
The combination of technologies enables printers to easily achieve flawless, perfect print quality for their customers. Valuable production data and detailed print quality reports can be used to improve print shop processes and produce more jobs per press. This saves press time and potentially reduces the need for additional presses.
John Cusack, business development specialist at Baldwin Vision Systems, explains: “More and more customers are demanding 100% print inspection and detailed print quality reports. With Defender, printers and converters can monitor and improve processes and directly increase their profitability. The right tools to detect and correct errors also reduce the risk of returns, complaints, lost business opportunities and damage to reputation. With Defender workflow, printers can meet customer expectations, retain existing customers, develop new markets and win new customers through a clear competitive advantage.
The Defender workflow includes the following components:
Defender 100% Inspection uses the industry’s most advanced defect detection algorithms to quickly classify defects and make better print quality decisions. Unique self-learning algorithms monitor press performance and automatically apply the optimum inspection tolerances to each job. Job settings can be changed and saved with minimal effort. Manual fine tuning of sensitivity levels for specific defect types and substrates enables false alarms to be largely avoided. State-of-the-art, highly efficient LED lighting with active cooling ensures more print image detail with low image noise.
Defender Data Central offers smarter print inspection with visual maps of each inspected roll. Quality control staff can analyse the number, distribution and type of defects. Out-of-tolerance areas are identified for removal, and quality reports can be generated on a job basis.
Defender Waste Manager can be connected to rewind, slitter and sheet slitter devices to automatically control stop and ejection, making it quick and easy to remove faulty material. Defect location data allows the exact location of the defect to be quickly located.
All Defender components are controlled via powerful yet user-friendly touch screens, requiring very little operator training. New users can familiarise themselves with the app-style system in minutes, reducing the need for highly skilled personnel.
“Our advanced, data-networked workflow enables strategic decisions to be made based on facts,” explains Cusack. “With the tracking workflow, all defects can be corrected before delivery, so the customer receives a perfect product. In addition, it is possible to decide which defects may not need to be eliminated based on the customer’s specifications. This ensures maximum yield and profitability for every order”.