Finishing & Screen Printing
Former-Navy BOBST personnel oversee a challenging relocation project for our customer
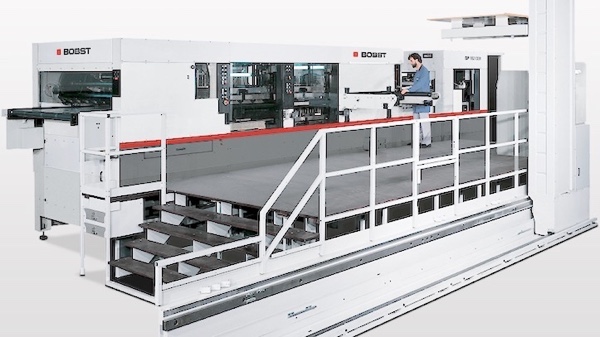
Thursday 27. August 2020 - At 41 feet in length, 27 feet in width and 12 feet in height, the BOBST SP 162 CER is a very sizeable die-cutter. Its sturdy construction supports its highly reliable rates of production, enabling delivery of die-cut, fully stripped, separated, stacked, and batch counted cartons, hour after hour, day in, day out.
Which is great when installed but causes some problems when you need to relocate it! At 75 tons – which is the equivalent of about 15 elephants – it is a seriously heavy piece of equipment. Moving one would be difficult enough. But what about relocating three, to separate locations across the United States?
That is exactly the challenge a leading designer and manufacturer of packaging for commercial products faced. With the expansion of its machine fleet, no Navy pun intended, they needed to relocate three BOBST SP 162 CER machines from their site in Northeastern United States, to three other sites in various locations across the continental US: the furthest being in California.
BOBST was contacted to oversee the relocation, which when it comes to state-of-the-art machinery like this, requires specialized expertise.
Navy veterans ensure project stays afloat and keeps on course
Overseeing the project were Danny Sides, Strategic Account Manager at BOBST, and Brian Ewart BOBST TSS Installation Specialist. Coincidentally, both are US Navy veterans, and it is just as well, because this relocation was as strategic as a military operation!
“It was great working with Brian on this project because we have very similar Navy background and could apply the same level of military-style planning and calmness to a very challenging project,” said Danny Sides, “I go into any challenge believing it is solvable and just breaking it down into one obstacle at a time. This pragmatic and composed decision, is why I believe we did a great job on behalf of our valued customer.”
The BOBST relocation team faced several challenges. However, none larger than having to coordinate the logistics for these large-scale moves, all the while maintaining the health and well-being of the technical crews during a worldwide pandemic.
Another unique challenge was that one of the machines had not been in operation for a great deal of time: parts had been removed from it to perform critical repairs on other equipment. This required a thorough diagnostic job by the BOBST Field Service Technicians (FSTs) to identify missing parts and ensure they were ordered and sent to the team at the machines new location.
“The real heroes of this story are our FSTs who had never seen this exact machine before in their lives. But with a herculean effort, they were able to piece it all back together and get it production-ready in the space of only 16 days,” said Danny. “Whatever the situation, our team is solution focused and committed to helping our customers. I could not be prouder of the FSTs on this project.”
The first machine is now successfully relocated & installed and the other two will be relocated shortly. In the meantime, our customer continues to purchase many new pieces of Bobst equipment to modernize their productivity and increase their future competitiveness.
“I think a project like this demonstrates the commitment and dedication of our BOBST employees and the impact we have on our customers,” said Danny. “We really care about the work that we do and the people it affects. Its more than just a job. Well always go the extra mile when we need to – and in the case of this relocation, we travelled many miles indeed!”