Finishing & Screen Printing
How BOBST is helping ITASA to take silicone coating to the next level
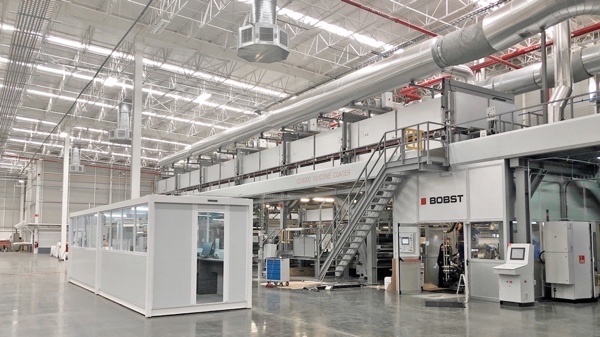
Tuesday 26. May 2020 - Jaime Espinosa, General Manager at Itasas new production facility in Queretaro, Mexico, is talking about the company philosophy. Itasa - which is headquartered in Spain - has been manufacturing high quality release liners for a variety of applications and industries since 1974. Today the company is considered a global reference in the release liner market.
“We always say that reliability means confidence. The key to reliability is the production process and its control. A controlled process ensures quality. This is reflected in the consistency of our products.”
“We are very proud that Itasa is amongst the biggest players in the commercial silicone coaters space,” continues Espinosa. “But it is a competitive industry and we can never stop investing and looking for the next innovation. Thats why we turned to BOBST.”
Enter the CO 8000
BOBST shares Itasas philosophy of achieving the highest quality through optimized processes which is why Itasas Mexico division has recently invested in a BOBST CO 8000 silicone liner machine, configured for solventless thermal silicone coating on paper and film and featuring BOBST solutions for perfect process integration and seamless workflow. These include an inline flexo printing unit with a print repeat up to 1200 mm, a sleeve system for fast job changes on both anilox and print cylinder, integrated ink viscosity control and dedicated floatation dryer suitable for both water-based or solvent-based inks.
However, arguably the key benefits of the machine lay with the process critical issues, such as the quality of coating and drying at high speed, paper re-moisturizing and web handling capabilities, especially at the rewinding stage, which is quite complex with siliconized materials.
Custom-built for custom tasks
“This machine was custom built for Itasa, and it is easy to see that great care has been taken to ensure the right match between our needs and the capabilities of the equipment,” said Espinosa. “We will benefit hugely from the quick reel changes, quick set-up times, precise tension and speed regulations, as well as a high level of electrical and mechanical availability.”
The CO 8000 is an ideal solution for converters who need high performance tailor-made production lines. For film manufacturers, it is the perfect solution for added-value products, such as barrier coatings for flexible packaging films. In the paper industry, silicone and adhesives coatings are mainly used in the production of industrial tapes, labelstock and hygienic products. For these applications BOBST delivers customized lines based on the specific needs of the application required, coating weights and viscosities.
“One of the key changes that we have seen in customer requirements in recent years is the increased focus on optimized coat weights, automatic inspection and minimization of surface defects, lay-flat properties, and more stringent release force tolerances,” says Espinosa. “The CO 8000 helps us to fulfil these needs. In addition to the flexible concept of the coating unit, and the construction quality, we were particularly impressed with the seamless integration of the flexo printer. We also took into consideration BOBSTs technological capabilities and service infrastructure.”
BOBST takes great pride in providing comprehensive services for its clients. Completely hands on during installation and training, BOBST also offers in-depth inspection services and machine upgrades, remote diagnostics and monitoring, training courses and specialist production process improvement advice.
One eye on the future
“There is no doubt that BOBST designs and manufactures state-of-the-art equipment,” said Espinosa. “This supports us in our goal to focus on our customers, offering them the best service with maximum flexibility and personalized solutions. As for what is next, recyclability and sustainability, as well as certification of paper sources, are increasingly in focus for our customers and end-users.
These topics are on top of the industry agenda and we are working to develop new solutions. Overall, we see a strong market potential and increasing demand. The project in Mexico has been very well received by the market and we are confident that we will build a second silicone coater in the near future.”