Inkjet & Digital Printing
Dynamic technology: direct printing on cylindrical objects
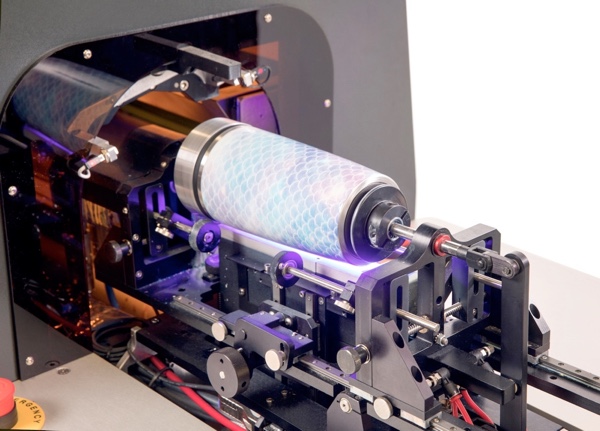
Thursday 13. February 2020 - Direct printing of cylindrical round bodies is a relatively new application that opens up a whole spectrum of possibilities. Digital printing techniques (optimized with special inks and advanced print heads) have been integrated into automated production processes to achieve impressive, reproducible quality at low cost. The result is expanded business potential for print service providers and new opportunities for customers in the areas of branding and advertising campaigns.
By Benjamin Adner, CEO Inkcups
First a definition: Direct-to-Object (DTO) printing is the application of ink directly to a curved surface, usually the wall of an object, which has a circular cross section and a constant, conical or variable diameter. Printing on cylindrical objects is possible by pad printing, screen printing or digital printing.
Pad printing is suitable when the job is produced with one or two colours and only one or two colours are to be printed on a limited area (no all-round motif and typically less than 25% of the surface). Screen printing can be used to print multicoloured graphics 360° all around surfaces. Screen printing has the advantage that it is widely used and is a proven process. However, the disadvantages are the required working time, material costs and additional production steps. Today’s demand for additional colour and more creative image reproduction options for cylindrical objects is driving screen printing away from more efficient and feature-rich digital systems.
Digital DTO printing offers three key advantages over screen printing: 1) the ability to produce multi-colour and/or full cylinder design effects in a single pass; 2) the ability to print short runs with personalisation; and 3) enormous time and cost savings. Taken together, these strengths speak for digital DTO printing.
In this article we will focus on the newer digital process.
A wealth of applications
While digital printing on flat objects has been common practice for years, users can now digitally print a wide range of cylindrical objects. It should be noted, however, that many machines on the market are subject to restrictions regarding the type of cylinders that can be used. The most important parameters in this context include the diameter and length of the object, the cone angle if applicable, and the depth of the largest contour. In addition to limitations of the digital printing system, users should also consider the material composition of the objects, as certain inks only adhere sufficiently to certain materials.
The variety of cylindrical objects that can now be digitally printed includes beverage glasses and bar accessories, stainless steel drinking cups, plastic sports drinking bottles, candles and candleholders, industrial sleeves, disposable cups, beer and liquor bottles, measuring cups, event products (e.g. water bottles for races), personalized items and cosmetics containers. The process is also suitable for printing on a wide variety of materials such as glass, coated metals, stainless steel, various plastics and paraffin wax (candles).
Glass objects are becoming increasingly popular. To ensure successful results, glass objects must first be flame treated to remove impurities and any coatings/refinements from the surface. A primer is then applied to ensure proper adhesion of the inks. Magicoat from Inkcups is an excellent glass primer for this purpose. Other DTO-printed cylindrical articles that are in vogue are hard plastic drinking bottles (Tritan) and bicycle drinking bottles – especially the highly compressible versions – whose printed image must survive hundreds of uses. Digital printing inks for ink cups are highly durable and abrasion resistant (e.g. up to 500 rinses for glasses) and meet international ASTM standards for adhesion.
Variety of colours and designs
The ability of DTO digital presses to print in full color in one pass and apply additional coatings and special inks allows a wide variety of design techniques to be used. These include:
– Mirror printing – printed colour images are visible on the inside and outside of glass or transparent plastic
– tone on tone – solid material with a matt surface is enhanced with a colour or transparent varnish
– Coloured glass – glass that is printed in colour so that it is still transparent
– Relief effects in which the entire image or parts of it are applied in several layers so that the print motif can be felt by the user
– printed images that simulate frost or etching effects
When printing the entire surface of a cylindrical object, seamless borders without visible overlaps are also important. For additional flexibility and easy file creation, the original artwork should be printable on cylindrical and conical objects without additional processing or distortion, i.e. flat images are printed to scale on a curved surface, with software automatically making the necessary adjustments. The best machines available on the market fully meet these requirements.
Full-color DTO digital printing is a faster process than screen printing, thanks to a smaller number of production steps. Multi-colour and more complex jobs require shorter makeready times, which means that shorter runs are possible. This means that users can better manage their inventory by printing smaller quantities on demand. They can also respond appropriately to time-critical jobs, such as jobs that need to be completed quickly in connection with sports competitions, events or celebrations. This not only shortens product manufacturing times, but also significantly reduces inventory costs and scrap rates.
What it all comes down to
When looking for a DTO digital printing solution for cylindrical applications, the types and materials of the objects to be printed and the range of colours and design techniques that users want to use should be considered. Not all pretreatment methods and inks are the same, so their quality and durability on different objects should be investigated and clarified. In this respect it is always a good idea to ask for test samples. The supplier of a DTO digital printing solution should know the specific market requirements of the interested user and should offer testing facilities, application instructions, direct sales support and expert technical advice.
By considering these aspects and working with the right partner for hardware, consumables and service, attractive and profitable new business opportunities in DTO printing can be developed.