Consumables
Castle Graphics prints with Azura plates
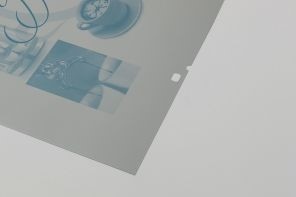
Wednesday 23. September 2015 - "Azura has helped us do more business with really demanding customers", Stan Alford, co-owner
Castle Graphics is a small printer based in Kyalami Business Park in Johannesburg, South Africa. It was originally founded in 1998 as a traditional repro house producing film for numerous customers in the print industry. In 2002 the company ventured into digital print with the purchase of a digital press. In 2006 they purchased a Heidelberg MO litho press with a Screen CtP system.
Castle Graphics is a close-knit company that was successful through the years. The owners and staff pride themselves on quality and service, and on the fact that they offer their customers a unique intimate service and are not afraid to tackle any printing project.
10+ Years of Azura
To celebrate more than a decade of the world’s leading chemistry-free printing plate, Agfa Graphics puts twelve users from all over the world in the spotlights between September 2014 and September 2015. Each of these customers also receives a customized celebration cake.
The company offers full color and black-and-white printing, as well as personalized print jobs, and large-format printing for POS and retail. They also execute DTP jobs such as scanning, retouching, lay-outing etc. Examples of print jobs include retail flyers, magazines, invitations, inserts, folders, brochures, menus and event material. Castle Graphics also offers a wide range of finishing options including saddle stitching, PUR binding, lamination, die cutting, laser cutting etc. Typical customers are supermarket retailers, advertising agencies, major restaurant chains, corporate and private customers as well as print brokers.
When asked for the key to their success, co-owner Stan Alford says: “We are small and give our customers a very personal and focused service with short delivery times. In order to be successful in today’s market environment we definitely think that you need a blend of litho and digital printing. Having this has definitely assisted us in our growth since 1998.”
Castle Graphics
Castle Graphics started using Agfa Graphics Azura TS printing plates in 2010. The company had been using Agfa Graphics’ Thermostar P970 printing plates before, in combination with chemistry and water. “Our biggest issues were probably the maintenance of the bath as well as the cleaning of the processor,” says Stan Alford. “We constantly had to check the status or strength of the chemistry in the processor bath to ensure that we got a good plate for the press.”
The switch to Azura TS went smoothly. Alford testifies: “The installation of the Agfa COU was hassle-free as it requires no plumbing. We are really satisfied as we no longer require a processor using chemistry. The variability of chemistry has been eliminated and we are guaranteed a good plate for the press as we only use a gum to wash the plate out. As a result, the number of plate remakes is negligible. On the press we have noticed a definite reduction in the make-ready time and sheets of paper.”
Castle Graphics
When discussing waste generation, Alford says: “I cannot believe how this has changed for the better. First of all, we need no more chemistry. In addition, we definitely noticed a massive saving in water too, where previously we were using vast amounts of water. Gum consumption is minimal and energy consumption has gone down too. Maintenance of the system is very little as there is no chemistry or build-up in the bath. Cleaning times are drastically reduced.”
Alford adds more words of praise: “We love the ease of use and stability of the system. Plates come out press-ready and are absolutely stable on press too. Thanks to the great image contrast of the plates, they are perfect for a visual inspection before getting to press. The image quality is excellent.”
Thanks to the combination of above mentioned advantages, Azura has helped boost Castle Graphics’ business. Alford: “Azura has helped us do more business with really demanding customers who have very short turnaround times for printed material.”