Consumables
Faster and more sustainable
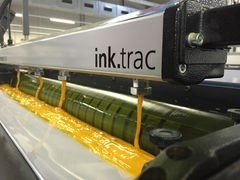
Friday 28. August 2015 - Effectiveness and environmental benefits thanks to automatic ink supply
Reduced workload during the work preparation phase, excellent cleanliness during the printing process and, higher environmental standards: especially in the case of high-performance printing presses, peripheral equipment offers numerous advantages compared to manual ink filling methods. At present, only a minority of offset printing companies are using automatic ink filling systems. When Peschke Druck from Munich relocated to larger production facilities, the company decided to automate their ink supply process with technology made by technotrans.
Until last year, manual ink filling processes were used by the employees of Peschke Druckerei GmbH. At high ink consumption levels, this was rather exhausting for the printers and so a new solution was required. Another disadvantage of the old method was the huge amount of waste created by the empty ink cans. With rising order volumes, the ink filling process became increasingly inefficient. However, automated ink supply systems were nowhere to be found at the Munich-based printing company – until the autumn of last year.
The relocation of the company to larger production facilities led Peschke Druck to review its processes. The company set as its goal the optimisation of the production layout in view of a sustainable business development. Peschke Druck built a new print building with a production area of 5,500 square metres. Since the relocation in the autumn of 2014, the entire printing process takes place on a single level. Only the offices are located on the upper floor and the digital printing facilities are also separated from the rest. This was also the moment when Peschke Druck switched from manual to automated ink filling.
With this push towards automation, the company from Munich is still something of a rare find in the German printing market. The majority of the German printing companies still use manual ink filling processes. Only a small minority, among them the major players, rely on automated ink supply. Among the factors speaking in favour of automation is the high speed of modern printing presses, which the manual fillers can never keep up with, and also the higher production quality.
Patented solution for better ink quality
For Peschke Druck, the solution was rather self-evident. After the company had already successfully used the cooling and temperature control solutions made by technotrans, the decision in favour of the supplier and manufacturer with headquarters in Sassenberg was quickly made. Peschke Druck installed the ink.trac ink duct filling system into their existing three Heidelberg Speedmaster printing presses, two 10-colour type XL 105 and 106, which the company relocated to their new production facilities, in addition to a new 10-colour XL 105. After approximately six months of use, the company has drawn a positive conclusion: “It is quite a phenomenon how seamlessly the new technology could be integrated into our production environment,” says Thomas Scheder, head of engineering at Peschke Druck. “No malfunctions, no downtimes and, above all, an extremely high ink supply quality.”
The ink supply system consists of three components: (1) High-performance piston pumps in a pump station (2) feed the ink from rectangular 300 kg containers via a pipe system and (3) automatically to the ink.trac filling systems. A total of 20 of these are connected to the three printing presses for filling the ink ducts. The patented solution was specially developed for the central, fully automatic ink duct filling of sheet-fed offset presses. It is a plug&play solution with a modern design. The system comprises all of the components of an ink level control system; control unit with a display unit and control panel, sensor for monitoring the ink filling level, ink valve, and ink distributor pipe with special, low-drip ink outlets.
The supply lines for current (24 V), compressed air, and ink are all connected to the ink.trac units. Faults are indicated visually with the aid of a flashlamp. The printer can adjust the ink duct filling level easily at the push of a button via the display panel at the printing unit. The sensor monitors the filling level. If the ink consumption is high during a printing run, the sensor emits a signal and the valve at the ink.trac unit opens. As a result, ink will be supplied automatically by way of the ink pumps. An integrated flashlamp provides a clear indication if the ink.trac units fail.
Sustainability without ink can waste
“Peschke Druck strikes a new, sustainable path in terms of the ink supply with our automatic ink filling system,” says Ulrich Meitinger, sales manager of technotrans. “Printers who are still scraping ink out of cans with an ink knife should ask themselves whether they can really cope with increasing press speeds and a growing number of printing units per press.” Automation is the only way to avoid ink level variations in the ink ducts and the permanent monitoring of the ink level. At Peschke Druck, the advantages have already clearly manifested themselves.
Today, nobody fills ink into the ink ducts by hand at the printing company in Munich, as Thomas Scheder confirms: “By saving manpower during the refilling process, we can use it for more important tasks during the work preparation phase.” But this is not the only way that the ink supply is now much more efficient than before when it was still done by hand. ink.trac also offers numerous advantages during the change of shifts: In the past, the process had to be interrupted for the change of shifts, whereas today it runs continuously with a uniform ink level. The fact that the colour quality with uniform filling levels has also improved compared to manual ink supply is another benefit.
Another positive factor is the improved cleanliness of the printing press. When the ink fillers used to scrape ink from 2 kg ink cans into the ink duct, the printing press became soiled with ink residues. ink.trac, on the other hand, feeds the ink automatically and cleanly in a closed system into the ink ducts. The result: no ink residues. In addition, Peschke saves money when buying ink in large containers.
It was mainly the self-imposed commitment to a higher environmental standard that incited the Munich-based company to invest in an automated ink supply system. In the past, the company used to dispose of the waste cans in cardboard containers – an enormous cost factor. Since ink residues in cans are prohibited by law, the company faced frequent problems with the disposal company. Today, the ink supplier takes the rectangular containers back and refills them. Thanks to the technotrans solution, less than 1 kilogram of ink remains in the containers, which is only approximately 0.3 per cent of the delivery quantity. With the current order volume, the printers change the ink containers once or twice per week. All this without any costly disposal!