Business News
Technological milestones from Saxony revolutionised the press engineering industry
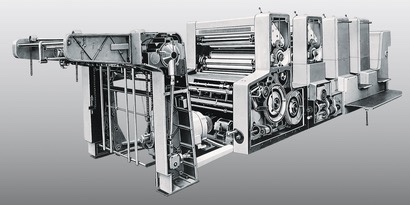
Friday 26. June 2015 - 50 years of unit-type sheetfed offset presses from Radebeul
Some 50 years ago most colour prints had to be passed through the press several times. On the one hand predominantly only one or two-colour presses were available and on the other hand from a technological point of view the prints required up to 12 colours. The establishment of the “short” colour scale (BCMY) in offset printing made production more rational on four-colour presses. These widely available presses were, however, a combination of two two-colour presses in a tandem design in line with the five-cylinder principle. This resulted in shortcomings with regard to press technology as every two printing units used a single impression cylinder. This type of construction also meant a huge amount of effort for press manufacturers, especially when it came to large-format presses. After assembly and print tests at the manufacturers’ plant, the machines then had to be taken apart again to a large extent and the many single components had to reassembled a second time when it reached the customer.
1965: Sensation at the spring trade fair in Leipzig
At the beginning of the 1960s engineers at the Planeta press plants (a member of the KBA group as KBA Radebeul since 2001) thus toyed with the idea of building a press without all of these grave disadvantages. The switch from the tandem to today’s dominating unit-type design for sheetfed offset presses began with the launch of the Planeta Variant P4 (B3 format) at the spring show in Leipzig in 1965. The future-focused design was even applied to large-format presses from Radebeul only two years later. The world first from Saxony 50 unveiled years ago was one of the technological milestones which fundamentally changed sheetfed press engineering and today is widely used by a raft of manufacturers.
Pros of the unit-type design
The unit-type design was then a completely new and revolutionary press design in line with the three-cylinder principle. For the first time the individual parts and the technical properties were identical in every printing unit. This offered a raft of advantages which today still apply to all subsequent presses in the Planeta Variant series up to the cutting-edge KBA Rapidas:
High level of flexibility when it comes to tailoring a press’ configuration to the needs of a printing house
Significant reduction in the number of different parts when producing the press
Short assembly time at the customer’s given the delivery of completely assembled parts
Accurate print register via a superior drive system
Smooth sheet travel given the first double-size impression cylinders and transfer drums
Lower number of sheet transfer points between the printing units
Outstanding dot-sharp reproduction compared to other presses.
Convertible perfecting in one sheet pass (Planeta patent from 1967) is also based on the unit-type design. While it was only possible to place an imprinter in front of the first printing unit with the tandem design, perfecting on a unit-type press is possible anywhere. The prerequisites for today’s eight, ten or twelve-unit presses for 4/4, 5/5 or 6/6 printing and indeed other special configurations were thus created back then.
New technology opens up new possibilities
The new technology with double-size cylinder systems opens up completely new possibilities for printers in terms of print quality and substrate flexibility. The streamlined, smooth sheet travel delivers significant advantages especially for cartonboard printers. Accordingly, the Variants and Varimats from Radebeul were installed in a raft of packaging plants worldwide at an early stage. Thus the foundations for the press manufacturer’s leading position in folding carton printing were laid half a century ago. This is also true for today’s cutting-edge high-tech Rapidas. KBA Rapidas are the first choice for printers of heavy board, beer mat board and corrugated. Furthermore, large-format Rapidas printing units are also implemented into KBA Metalstar metal-decorating presses. It is not without reason that KBA is the global market leader in large-format packaging printing presses. The unit-type design can also be found at KBA in superlarge format 150 x 205cm (59 x 80.7in) with the Rapida 205 launched in 2004 as the world’s largest sheetfed offset press.
The unit-type row design was also the prerequisite for the flexible integration of coating, drying and other finishing units in presses that are becoming increasingly longer. It delivered the huge level of flexibility in terms of printing and finishing equipment in sheetfed offset presses that is now standard. Sheetfed offset presses have become even longer since then. A KBA Rapida 106 in Switzerland holds the world record with 19 printing and finishing units.
The fundamental ideas are still in place today
It goes without saying that the basic inventions have been updated regularly over the last 50 years and brought up-to-date technologically. Today’s standard production output of up to 20,000sph on the Rapidas and extensively automated printing and makeready processes were still unheard of in the 1960s. The Planeta Variant P4 was engineered for 10,000sph and nonstop operation for 8,000sph, half as fast as the KBA Rapida 106. The speed and makeready world champion in medium format even permits job changes on the fly (Flying JobChange) without stopping the press.
Photo 6: Rapida 145
Packaging printers still profit today from the streamlined sheet travel with double-size systems developed in 1965. Printing on board, corrugated, beer-mat board and even metal is no problem for properly equipped Rapidas (6)
All leading press manufacturers use the unit-type design with the usual modifications in their sheetfed offset presses today. In our fast-paced world it is easy to forget that it was the clever engineers from Saxony who first had this ground-breaking idea and that it often took decades for others to adopt it. Nevertheless, this often happens in the history of technology.