Offset Printing
Quick, precise, reliable – InlineDensity Control for newspaper printing
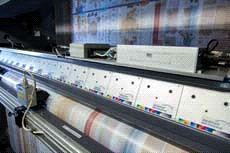
Thursday 16. October 2014 - New, fully integrated color control from manroland web systems
A new product based on a wealth of experience: “InlineDensity Control with micro-marks” – IDCµ for short – for newspaper printing. manroland web systems has been constantly upgrading ink density measurement for commercial printing. Now the fully automatic color control IDCµ will also offer unprecedented process stability for newspaper printing.
The inline color control “InlineDensity Control with micro-marks” (IDCµ) already enjoys the trust of customers. The future COLORMAN e:line user Jörg Schild-Müller, Managing Director of the German media group Oberfranken GmbH explains the reasons for this trust: “I have been familiar for many years with InlineDensity Control for heatset web printing on our LITHOMAN. In our opinion, it is the fastest and most stable system on the market. Based on our positive experiences, we also want to use the system for newspaper printing. We are convinced that the manroland technology offers a decisive advantage, especially when it comes to the speed of measurements and control.” Dieter Betzmeier, Executive Vice President Technology and Project Execution at manroland web systems, explains the high demands placed by manroland web systems on ink density measurement: “Our inline measurement is the fastest and most precise system on the market, with full integration into the central control console and support around the clock.”
IDCµ for precise measurements
IDCµ ensures high print quality. Conforming to standards, the inline measurement of ink density offers premium quality and allows the printer to quickly regulate the ink supply. As Betzmeier observed during the development: “Inline measurement must achieve excellent quality within a short period of time, this is easily accomplished with IDCµ.” How will the new development be implemented technically? First-grade elements are used for the hardware. The cameras, from grapho metronic in Munich, are equipped with CCD sensors. Designed for high dynamic volumes, they can precisely measure small tonal value differences thanks to their polarization filters. Illumination is adjusted to specific standard filters through LEDs and suitable color filters offering long term stability. Measurements are carried out using a 45-0-geometry conforming to standards. The print copy is illuminated at a 45° angle and viewed by the sensor at 0 degrees to avoid direct reflections of the lighting on the optical measurement equipment.
Reliable control with IDCµ
The reliability of the InlineDensity Control improves process stability. IDCµ is virtually maintenance-free and offers a less complex workflow. With the conventional “image-based measurement” method, ink metering for individual colors in multiple superimposed printing is difficult to establish. This is only possible with a time and material-consuming calibration process that uses test prints to determine ink metering for a specific printing ink and a specific type of printing paper. In comparison, IDCµ does not require elaborate teaching, is not linked to the prepress and does not affect the prepress workflow. Measurements are independent of the applied pressroom products and not affected by a change in printing conditions. This considerably lowers operating costs, increases operational reliability, and ensures sound ink metering control.
Full quality control
Offering the highest degree of integration on the market, manroland web systems enables efficient newspaper production. IDCµ is part of this quality package of inline control functions for ink density, ink register, cutoff register, fan-out and lateral web offset. The aim is to use a single inconspicuous micro-mark set for each ink zone position to cover all inline control features. These, including the new IDCµ, can be retrofitted in all newspaper offset presses.
Target value adjustment directly on the control console
Densitometry conveniently under control: With IDCµ, the printer can fully automatically implement the target value adjustment on the central control console. The PressManager provides the required order parameters. This takes place, for example, via the SlidePad or the ink zone keys, with a view of the print product, which offers a clear ergonomic advantage. With the other systems on the market, changes of the ink metering to adjust the printed image are more complicated and less intuitively applicable. The PressQuality reporting module subsequently evaluates the ink density measurement and, in addition to quality assessments, also displays all production events of the press log book.