Offset Printing
When only the highest hot foil stamping quality will do – was the focus of the MASTER-Hot Foil Stamping Day at Bobst
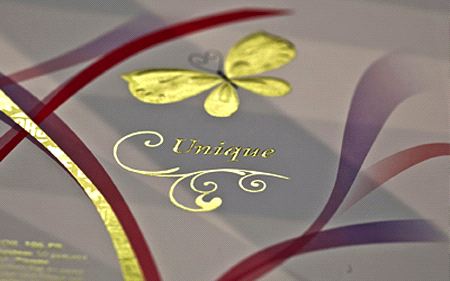
Monday 11. April 2011 - 'When only the highest hot foil stamping quality will do' - it was under this motto that some 40 experts from the German-speaking countries met at the COMPETENCE CENTER of Bobst SA in Lausanne-Mex, Switzerland, for the 'MASTER-Hot Foil Stamping Day' on 31 March 2011.
Without exception, they represented companies that impose particularly high demands on this type of print finishing and were only too pleased to have the opportunity to talk to each other about the latest trends on the market. Attention focused on innovative technologies in hot foil stamping that set new standards in terms of quality, productivity and cost-efficiency, as well as on new applications in trademark protection or the security sector, for example. The partner companies of the one-day ‘summit meeting’ of the industry were Hinderer+Mühlich with stamping dies, Kurz with hot stamping foils, and Sappi with paper and board.
The ‘MASTER-Hot Foil Stamping Day’ began with a number of short presentations by the experts from BOBST and the participating partners. Two developments, in particular, were high-lighted in this context. In view of the steadily growing pressure of competition, manufacturers of branded goods need to differentiate their products even more clearly and efficiently. The quality and creativity of their packaging plays a key role in this respect. On the other hand, they have to guard themselves against trademark piracy more than ever before, meaning that they must always be one step ahead in terms of technology. The more difficult and complex it is to imitate packagings, the more likely it is that forgers will be deterred and pirate copies detected. One of the subjects discussed at the ‘MASTER-Hot Foil Stamping Day’ was thus how challenges of this kind can most effectively be met using innovative technologies.
Four particularly demanding jobs served as examples to illustrate what is currently state-of-the-art and technically feasible in hot foil stamping – including two sample jobs for the new MASTERFOIL 106 PR high-end hot foil stamper. The experts from BOBST had prepared one job from the tobacco industry and one from the cosmetics industry for this machine, both of which were very similar to concrete practical examples. One job involved the application of a high-quality, silver hot stamping foil to 30 cigarette packs per printed sheet – from a large foil web, across the full sheet width, with a foil advance of more than 700 mm. Among other things, the pack design included relatively small, circular motifs, around which the silver foil was stamped. Not even the slightest register deviations between printed sheet and foil were visible. The other foil stampings were likewise fitted perfectly into the cut-out areas of the printed images. Operating at a speed of 6,500 sheets per hour, the MASTERFOIL 106 PR clearly underlined that it is capable of meeting such demands with relatively low pressures and temperatures. In the second job, ultrafine, miniature lettering was realised directly adjacent to deep blind embossing and microstructure stampings with gold foil in a single pass on 15 blanks of a perfume bottle packaging at a speed of 8,000 sheets per hour.
The MASTERFOIL 106 PR pushes back the limits in terms of precision, productivity and cost-efficiency, while at the same time displaying ground-breaking innovations as the new BOBST flagship for hot foil stamping. The revolutionary Foil Touch System is the highlight in this respect – a completely newly designed beam with innovative lower beam cam movement that permits 50% longer contact times between foil and printed sheet than any other machine on the market, even when working at maximum production speeds. Outstanding results are guaranteed for any type of foil application – be the stampings simple or combined with blind embossing, large or very fine. The Power Register II dynamic register system, in turn, ensures perfect registering between print and foil. The first Smart Feeder to be used on hot foil stampers to date reduces the number of stops in the feeder by up to 70%. The MASTERFOIL 106 PR processes papers upwards of 70 g/m², board up to 2,000 g/m² and even corrugated board with a thickness of up to 2 mm. Additional features are 25% shorter set-up times and particular cost-efficiency. “It wasn’t at all easy to get our guests away from the machine and on to the other demonstrations,” said Volker Claus, responsible for hot foil stampers at Bobst Group Germany, summing up the enthusiasm of the visitors for the machine and the sample jobs shown.
But attractive sample jobs were also waiting on the other machines. For example, the SP 76 BM addressed the subject of protection against trademark piracy and safeguarding the authenticity of products on the basis of a pharmaceutical packaging. In addition, an interesting niche application was to be seen on the EXPERTFOIL 104 FR, where embossing with silver foil was realised on a cosmetics gift box on printed sheets of N-flute board.
One participant formulated his personal verdict like this: “BOBST and the other manufacturers represented here in Lausanne put us on the right track when it comes to hot foil stamping. The presentations at the ‘MASTER-Hot Foil Stamping Day’ left no doubt about that. I, for one, was greatly impressed by the performance of the MASTERFOIL 106 PR on the Unlimited cigarette pack job.”