Prepress
X-Rite makes press standardisation easy
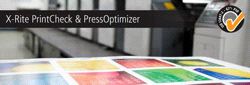
Friday 25. March 2011 - Standardization is a topic of growing importance for color printers, which is also increasingly required by print buyers. It can benefit internal efficiency, because there is less waste of time, energy and materials, while providing a valuable sales tool because it acts as a proof both of quality and just as important to many customers, consistency.
X-Rites PressOptimizer and PrintCheck have recently been released to help printers achieve and maintain standardization in a way that is easy for both operators and customers to understand. Developed jointly with color specialist GMG, they are automated software solutions that offer lithographic printers of all sizes an affordable and easily understood way to implement standards compliance.
They support the ISO 12647-2:2007 standards for commercial offset printing (with all five paper types), and ISO 12647-3 with the specifications for Newspaper 26 and 30, plus GRACoL 2006, G7, Japan Color STD 2007. They can also work with inhouse standards.
Wizard interface for ease of use
Previous print quality control systems have often been complex and hard to understand. X-Rite offers a Wizard-based user interface and menu structure that is very easy to understand, with clear step-by-step instructions. The built in knowledgebase/trouble-shooter even explains the basics, such as what standardization means and why it matters, and what ISO 12647 is. This ease of use makes the system particularly attractive to print company staff who may be implementing color standards for the first time, and it will also help their customers.
The programs generate easy to read but detailed reports, with important information presented visually as graphs and charts. Pass/Fail indicators are prominently displayed, with a large green dot for pass, or yellow for a warning that something needs checking. Printers can apply their own brand or logo and send the reports as PDF files to their customers.
PressOptimizer can be used with X-Rites 528 / 530 and SpectroEye LT / SpectroEye handheld spectrodensitometers, and also with the automated scanning instruments IntelliTrax or EasyTrax, to set up the presses to meet the desired standard, though the actual certification process will probably also require outside color consultants. Once the standard is achieved, then PrintCheck is used to verify that commercial print jobs are produced within the parameters that the standard requires. PrintCheck Review and PrintCheck Reader are additional utilities that can be used by print buyers, customers etc, to perform their own local verification of PrintCheck forms within their own offices.
PressOptimizer helps set the standard
PressOptimizer is used to establish and maintain process control and Standardization for one or more presses. It allows users to produce matching results from several presses, even older models, and allows repeat jobs to be set up rapidly. This program is best suited to medium to large printing companies, probably with several presses, with a need to set up press and paper combinations fairly frequently. Smaller printers would probably use an outside consultant for this stage, and then use PrintCheck internally to verify that commercial jobs are within the specification.
The Wizard based interface guides operators through the whole process, to analyze gray balance, measure tone value increase and spread, check primary and secondary colors, generate CtP correction curves for most Rips, control ink acceptance and determine the optimum print contrast.
Access the knowledge database
The main stages start with the definition of parameters for the work, including paper (printers can build up a database of the types they use) and the standard thats being checked against. As you create a new standardization job youre presented with a knowledge database with four main categories: standards, prepress, press and checklists. Standards is a general explanation of what the standards are for (especially ISO 12647-2). Pre-press looks at software and platesetting requirements, and the settings for the output of the test forms on plates (for inking, ISO and NPDC verification), plus the generation of verification wedges to run alongside commercial jobs. The press section gives instructions for maintaining and adjusting the offset press to get optimum results prior to the standardization form being printed. The checklist section is a briefer presentation of all the setup steps you need to go through, without the lengthier explanations.
Having gone through the parameters, you move to Job Management, where you enter the basics of the job: the press being used, the calibration method needed (such as ISO 12647-2), plate curves (linear or compensated) and ink type (conventional or heatset/UV). The window then shows the ink test form and explains it: for instance there are 14 sets of patches across the width of the form, equivalent to ink keys on the press.
You then make the plates, run the test job, and then return to PressOptimizer where you connect the measurement device. You read the form values when the ink is wet, and again after six hours, when it has dried. PressOptimizer calculates the best density settings for each ink color to give the minimum Delta-E (ie minimising the shift in colors from the ideal). Most standards require a Delta-E of less than 5, which would be undetectable to most human eyes.
All in the visual detail
The form patches are displayed on-screen and you can click on any of them to see its individual value. You can also click to see graphs displaying all the patch values. Therefore you can quickly move between “at a glance” overviews to very detailed analysis if you need it.
Next the TVI values (otherwise known as dot gain) will be assessed for the keys where optimal density was identified. If these are within the specification you see a big green button; if not it will be red. In the case of a failure, you click the red button, which automatically exports a calibration curve for the platesetters Rip.
You now use these to print a verification test form, which uses the newly calculated values. You measure this once again. If the values are within specification then you see a green button and can continue to use the CtP Rip compensation curves that were generated in the previous step. If the test fails, you again click the red button to generate a new compensation curve set, then re-output the verification form and test it again. This process of multiple tests and recalculation of compensation is called iterative, and is intended to get closer and closer to the ideal as represented by the standard.
The CtP compensation curves are then applied to future commercial jobs, which will then be in tolerance. This can be verified from day to day by using PrintCheck.
Printcheck for job verification
PrintCheck is a companion program to PressOptimizer, which reads the density wedges and other color information thats printed alongside commercial print jobs (as opposed to the special test forms that are read by PressOptimizer). It is used to verify that commercial print jobs are within tolerance and to analyse the reasons if they are not.
Its relevant for small to medium sized printing companies and can be used with X-Rites handheld spectrophotometers, including the 528, 530, SpectroEye, plus the press-side auto scanning IntelliTrax and EasyTrax.
Again offering a Wizard based interface, it uses a single measuring procedure to read (using the measurement instrument) then analyse all the relevant information for a print job. Theres a choice of “full check” and “quick check” options, depending on whether you want to use a job later to analyse trending or not. The quick check option performs a measurement only and displays the results immediately after that, whereas the full check requires the user to enter some basic data on the job which can then be used as filter criteria for trends across multiple jobs. The checks include print density and contrast, tone value increase and spread (ie dot gain), primary and secondary colors, gray balance, ink acceptance (ie trapping) and paper.
The information is presented within the program window as a series of menu icons. You click on each icon to view the particular data, which is shown as graphs or charts alongside the relevant numerical readings.
Historical performance review
It also allows users to compare jobs and view trends based on job histories and press performance.
An information panel within these windows gives basic information on the meaning of what they are displaying, and in most cases will offer a longer “troubleshooter” explanatory window, with general information and suggestions for quick fixes or mechanical fixes to problems.
Two particularly useful features are “Job compare,” which lets you load up to four previously saved jobs and would be useful for reprints; and “Trending,” which loads all previously saved jobs and can be used for longer term comparisons between presses, or between shifts. Comparisons and trends cannot yet be printed as reports so far.
Checking by print buyers
PrintCheck Review allows print buyers to run their own measurement checks on “press pull” job sheets. Its intended for brand owners, advertising agencies, publishers and packaging designers and can be used with the affordable X-Rite i1 Pro spectrophotometer.
Its easy to use even for non-experts, with the Navigation Wizard taking the user step by step through all the processes, so nothing can be overlooked.
Free data reader
PrintCheck Reader is a free utility that anyone can download from the X-Rite website. Aimed at print buyers and their end customers, it lets users import PrintCheck data that is measured by the pressroom and supplied to print buyers and customers. In other words, it is for people who do not need to own a measurement device, so they can analyse information provided by the pressroom.
Conclusion
Given X-Rites history its no surprise that PressOptimizer and PrintCheck can provide full technical measurements which are used to calculate the compensation settings needed to achieve and maintain the standards. What makes these programs particularly outstanding, though, is the extreme ease of use, so anyone can run them. As the printing industry continues to progress from craft to process controls, these programs can be valuable tools that can ease the adoption of standards by all sizes of offset company.