Packaging
Guaranteeing production flow consistency with BOBST
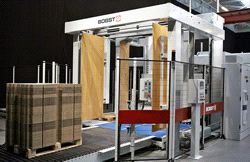
Wednesday 20. February 2008 - BOBST offers a complete range of peripheral equipment, including both semi and completely automated units from the loader to the palletizer, which complete their printing and die-cutting lines.
The LOADER, BOBSTs automatic feeder, which can work with our without pallets, centers the pile and using a motorized pusher and mechanical fingers, separates the entire pile, down to the last sheets, into batches from 40 to 250 mm high. When working with pallets, the empty pallet is evacuated and the following pile loaded. An intermediate table puts the last batch of the previous pile into a standby position so as to guarantee a continuous, high speed delivery of sheets to the feeder. The LOADER is suitable for all past and current BOBST flexo printing presses and SPO Autoplaten diecutters.
The G-BREAK blank separator and G-PAL palletizer ideally complement the BOBST SPO 160-VISION and SPO 160-S diecutters. Requiring minimal floor space and being highly flexible, they guarantee, regardless of the job, the separation of blanks and the formation of perfect and regular piles of finished product, thanks to an efficient squaring system on all four sides.
The peripheral equipment adapted for the MASTER product range, has been redeveloped to match the new production speeds of these high performance lines as well as to work with 300 mm high batches. The BREAKER separates individual blanks as small as 200 X 200 mm with a minimum of pressure so as to maintain the properties of the board and avoiding marking. The automatic batch arrangement after the BREAKER offers a choice of configurable modules, capable of meeting the most varied of requirements and integrating the product into the space available. The PALLETIZER guarantees the perfect regularity of piles, essential for automatic packing machines, and is achieved thanks to the squaring system on all four sides. The insertion of a sheet between each batch layer before palletization ensures the stability of the pile during transportation.
The market for corrugated paperboard packaging being demanding, each box supplier seeks the best possible means of working efficiently. In order to offer the most productive solution to its customers, BOBST concentrates both on the heart of the production line – the SPO press – and on the peripheral equipment, as together they contribute totally to ensuring the final result.