Prepress
SCREEN PLATERITE 8800 THERMAL PLATESETTER AND TRUEFLOW WORKFLOW SYSTEM STREAMLINE PRODUCTION FOR NEOPRINT, INC.
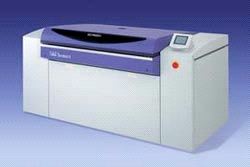
Wednesday 23. January 2008 - "We will get jobs, especially for our web press, that need to have 150 plates ready for the next day," observed Peter Holt, prepress manager. "We have to be able to output those plates and still accommodate the other work that comes in."
Like many printing companies, Neoprint, Inc. often deals with big projects that need to be turned around in a hurry.
“We will get jobs, especially for our web press, that need to have 150 plates ready for the next day,” observed Peter Holt, prepress manager. “We have to be able to output those plates and still accommodate the other work that comes in.”
When a burst of work requires the prepress department to deliver a large volume of plates on a tight deadline, the Chelmsford, Mass.-based firm’s fully automated Screen PlateRite 8800 thermal platesetter enables nonstop production.
“The PlateRite system is incredibly solid and reliable,” Holt said. “We never have to worry about it breaking down.”
Neoprint was formed by the merger, in August 2005, of Sullivan Brothers Printers and Northeast Offset. Combining the two well-established commercial printing operations created a single force dedicated to helping designers and print buyers capitalize on their communications opportunities.
The majority of Neoprint’s current production is high-end commercial work of four colors or more. Annual reports, brochures, point-of-purchase materials and newsletters are mostly produced on the company’s 40-inch sheetfed presses.
Neoprint added a six-color Komori Lithrone S40 equipped with coating unit in May 2007. The Komori press complemented an existing six-color Mitsubishi sheetfed, also with coater, and a Miller perfector configured for four-over-two printing. In addition, Neoprint operates small-format Heidelberg GTO and Ryobi presses.
Print runs average 10,000 to 15,000 pieces for multicolor work, although Holt noted that Neoprint turns around “a lot of jobs under 5,000 sheets.”
On the web side of Neoprint’s printing business, a Goss Suburban non-heatset press is used to print community telephone books, want ad catalogs, real estate guides and directories. Color covers for these jobs are printed on the six-color presses.
Holt said Neoprint keeps the presses fed with about 1,500 plates in an average month. “But sometimes there will be as many as 3,000 plates in a month,” he added.
The prepress department already was familiar with Screen imaging technology when it purchased the PlateRite 8800.
“We originally had a PlateRite 8100 that replaced an older imagesetter.” Holt recalled. “We went from making plates from one-piece punched film to outputting files directly to thermal plates. Upgrading to the faster PlateRite 8800 has further streamlined our process so we can work more quickly and efficiently.”
Neoprint opted for no-bake thermal plates. By doing away with preheating and postbaking, the plates cut processing times. Holt said the PlateRite 8800 averages 24 eight-up plates per hour as a result.
The PlateRite 8800 just as easily handles the plate sizes that run on Neoprint’s small-format presses. To satisfy the plates needs of the Ryobi press, the prepress department images GTO-size plates and trims them to the smaller size.
Screen’s Trueflow PDF- and JDF-based workflow management system drives the platesetter.
“Trueflow is an excellent workflow system,” Holt stated. “It can RIP any files our customers give us. The trapping and page imposition functions are exceptional and easy for operators to understand.”
The Screen organization earns high marks as well.
“Screen is a great company to work with,” Holt said. “The service response has always been first rate.”