Packaging
BOBST MASTERLINE: More value per square meter
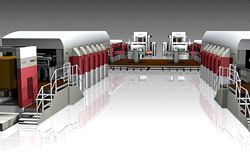
Monday 21. January 2008 - With the productivity of its customers in mind, BOBST introduces complete "mirror" lines for the production of corrugated paperboard packaging
Anxious to provide its customers with solutions that let them achieve their productivity goals, BOBST has launched a MASTERLINE production line redesigned as a mirror image of a standard configuration. Jonathan Abbis, responsible at BOBST for the SPO-FLEXO product line – corrugated packaging converting – says of the new line that, “In the world of corrugated paperboard, the trend among our customers is, as far as possible, to industrialize the manufacture and transformation of this material. They are constantly looking for solutions which can help them achieve their objectives of producing quality products, in increasing volumes, taking less time, and optimizing, wherever possible, productivity from a given surface area. The solutions which we have developed answer these needs and, in an optimal implementation, these MASTERLINE configurations can realize more than 5,000 square meters per hour of printed, diecut and palletized packaging.”
He adds that, “In a study of the needs of our customers, their desire to maximize both production per square meter and machine uptime was clear. We have met this requirement by providing customers with the possibility of laying out a pair of MASTERLINE as mirror images, creating a central working area from which the operators can intervene quickly on either machine. In other words, we can create a new solution for the integration of production equipment into the plant, providing more flexibility and more modularity “.
A redesigned line
For Mauro Chiari, responsible for mechanical R&D, this is an important development. “Until now, the operation of BOBST machines has always been from the same side so, to create this mirror version, we had to undertake significant modifications to the whole line. During the redesign, all of the components required considerable attention. For example, on the MASTERCUT diecutting platen we had to reverse all the controls, the sector, the double cams and the worm gear among other components.The heart of the mirror line is now on the left.”
Despite having just been launched, the mirror line has already confirmed BOBSTs expectations, with several sales already agreed and the first complete MASTERLINE mirror line due to start in production at the beginning of 2008.