Packaging
Swedish finisher SKYLT & FALS SOFI AB meets success with its BOBST COMMERCIAL 106
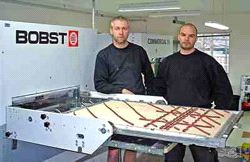
Monday 14. January 2008 - SKYLT & FALS SOFI AB is a family company owned by two sisters, Therese Reinholdson and Eleonor Lundblad, together with their husbands Pontus and Marcus. Based in Gothenburg (Sweden), a harbour city of around 600,000 inhabitants, the company has a further family pedigree having been founded by Thereses and Eleonors father, Roger Ankén, in 1966.
Today, the eight strong company provides, among other services, diecutting, creasing and perforating, mostly for commercial printers. SKYLT & FALS has earned a reputation for its ability to take on big runs, to meet short delivery times and to run a wide range of formats. The BOBST COMMERCIAL 106 diecutter has, says the company, contributed strongly to SKYLT & FALS recent success.
A former user of cylinder diecutting machines, last year the company decided to look for new solutions that would help them increase turnover and keep margins in house. To achieve this, SKYLT & FALS decided to develop their diecutting activities and began the search for a reliable equipment supply partner. Having heard about BOBSTs reputation for quality and reliability, the company got in touch with Curt Meixner at Bobst Group Scandinavia who arranged a visit to a UK plant to see a COMMERCIAL 106 in production. “Having seen this diecutter in action we decided it would be a waste of time to look for any other suppliers,” says Therese Reinholdson. “Without any doubt, the machine was the one for us and has proved to be precisely the solution we needed.”
With the COMMERCIAL 106, SKYLT & FALS are now able to convert everything from paper to thick cardboard and plastics. Run lengths now range from 5,000 to 20,000 sheets, with about 40% of the jobs being repeat work and 60% of the companys work now being run on the new diecutter.
When asked about the introduction of the COMMERCIAL 106 into the plant, Eleonor Lundblad says that it was much easier than she thought it would be to go from using cylinder machines to running an automatic diecutter. “It took us only about three months to reach full performance, during which time BOBSTs training and technical support was brilliant, as were our contacts with their Sales team. To date, which is less than a year since the installation, we have run well over 1,000,000 sheets through the COMMERCIAL 106”
The COMMERCIAL 106 has proved to be highly productive for SKYLT & FALS, allowing it to deal with a wide range of jobs, in various materials, and down to quite small formats. As a further consequence, the company has been able to take better control of overall quality because it is now able to process long runs in-house which in the past they had to subcontract. This also allows SKYLT & FALS to retain more of the margin from each job. “We have increased our turnover by around 120,000 a year since installing the BOBST COMMERCIAL 106 and we are expecting to maintain this level of increase in subsequent years,” says Therese Reinholdson.